3 Planning Considerations For A Small-Scale Food Processing Facility
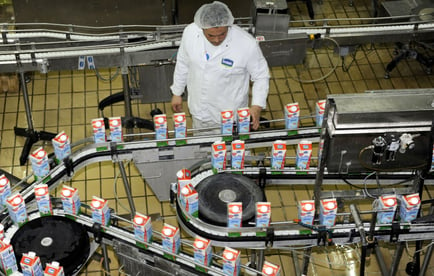
Food is an integral part of everyone's day-to-day life. Without food, you won't survive long, and neither will your neighbor nor the global population. That will lead to a significant reduction in human labor and the fall of institutions.
Similarly, if populations are fed with bad food, they can easily be wiped off the face of the earth, which will have similar effects as discussed above. That's why food hygiene and safety are the core of any food processing company. From the start of the company, that is, constructing the food processing facility, the company has to align all of its plans to meet the required standards for food safety.
This article will look more into food safety as a consideration for constructing a small-scale food processing facility. It'll also discuss other planning considerations, such as location and zoning regulations. Keep reading to learn more.
Food Hygiene And Safety
The federal government, specific city, state, and municipality govern the running of a food processing company. Regulations differ from state to state. These regulations also affect the construction of a food facility. For example, zoning regulations may allow or restrict the operation of a food company in a given estate according to building codes.
That said, the federal government's biggest concern is food hygiene and safety. The government established the Food and Drugs Administration (FDA), which ensures each processing company meets food safety conditions. Under the administration are laws such as Hazard Analysis and Critical Control Points (HACCP), which detail the procedures to be followed to minimize food contamination and the occurrence of biological, chemical, and physical hazards.
Another law is the Food Safety Modernization Act requiring that food safety be met through preventative measures. In this case, the company must avoid certain ingredients, storage methods, or distribution to avoid compromising food safety.
While this law may apply to the final product, their implementation starts from how the food facility is designed. For example, if the facility has an up-to-standard warehouse, food awaiting processing is less likely to be contaminated. Additionally, if the facility is damp, for example, an old house that has been revamped, there's a possibility that the dampness will cause food contamination through microorganisms such as molds.
When the food is contaminated, the processing facility risks being closed and you, the owner, being arrested and banned from handling food again for commercial consumption. Therefore, you want to make sure that you build a quality food processing facility to eliminate the risk of food contamination that might hinder your food safety performance when you start your business operations.
If you want to ensure that you comply with the laws discussed above, you can check TDI Packsys website for their automated inspection services.
Location
When choosing the location where you will establish the facility, there are several things you should consider. They include:
- The neighborhood of the facility: Look at the property that will be surrounding your soon-to-be food processing company. If the facility is in a rural area, consider the neighboring farms, if any. Will the pesticides used in the farm compromise food safety in any way? If yes, come up with mitigation measures to solve such problems. For example, you can ensure that the facility is properly sealed. Alternatively, you can change location to an area whose irrigation and spraying methods don't significantly impact the company's operations.
The same strategy applies if the site is in an urban area. Always look out for external factors that would impact the company's operations. Once you identify the factors, develop mitigation measures and test to see if the measures are working. - Access roads: Consider the ease of movement for the raw materials into the facility, finished products out of the facility, and the staff. It's advised you choose a site area that is easily accessible. Moreover, the area should preferably have an all-year access road. That is, the quality of the road isn't affected by seasons. However, if you'll be transporting your food using glass containers, a tarmacked access road will work best. With a smooth tarmac road, you'll avoid breaking goods that would otherwise mean an added cost to a small facility. Remember, the greater the expenses, the lower the profits; hence the slower the facility's growth.
- Nearness to raw material and market: One of the surest ways to keep your small business sustainable is by cutting costs as much as possible. It will work in your favor if you establish your facility close to the source of raw material and market. This will help you cut on the cost of transport, which promotes more profits and growth from the small facility.
- Water Availability: Water is essential for ensuring hygienic conditions for the facility are met. It's also an ingredient for food processing, depending on the type of food. Therefore, if you can get the water as a free resource from the site, it'll go a long way to reduce your operation cost since your only cost will be cleaning the water. However, if there's no water, you may have to purchase a regular water supply and storage.
Other than water availability, check for any potential water contaminants upstream. In case the water is polluted, you can clean it on a small scale by using chemicals such as hypochlorite, heating, using ultra-violet light, and filtration. - Electricity: Electricity is the backbone of all your operations. Without power, you won't be able to process your food or package it for supply. Therefore, when selecting a site for the facility, always check on power availability. The area should be well connected with electricity and have a few cases of blackouts. However, it's always recommended that you have a backup generator in case of power shortages.
Local Zoning Regulations
The last thing you want is to start your construction, only to find out that the zoning regulations don't allow food processing companies in that area. To avoid such issues, check on the zoning regulations once you have identified your site of choice. The rules will determine how big your food processing plan can be by looking at the building codes. For example, does the drainage system in the area support the volume of activities from a small food processing facility?
Besides building codes, zoning determines the number of employees you can have. In this case, since your facility will be small, you may not necessarily have to worry about that. Additionally, depending on your state, the zoning regulation may determine the design of your food facility. For example, some states may allow building your facility from an existing kitchen, constructing a new facility, or rehabilitating an old house.
To Sum It Up!
Although you should consider many other factors when planning for your food facility, the three discussed factors are the core of your plans. With the three figured out, you're better placed to start with the construction of your facility.
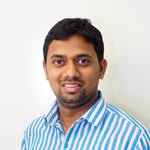
Ravindra Ambegaonkar
Ravindra, the Marketing Manager at NY Engineers, holds an MBA from Staffordshire University and has helped us grow as a leading MEP engineering firm in the USA
Join 15,000+ Fellow Architects and Contractors
Get expert engineering tips straight to your inbox. Subscribe to the NY Engineers Blog below.