5 Latest Tech Upgrades to Increase Safety in Manufacturing Facilities and Warehouses
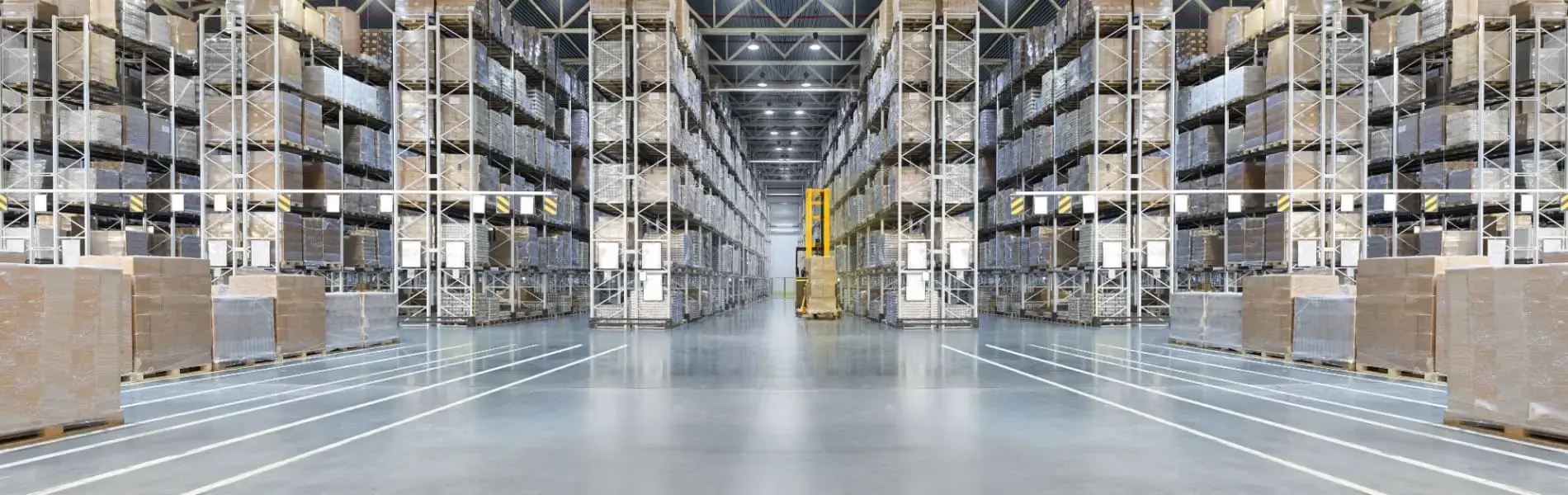
Despite the broad safety standards and regulations, workers' safety is a big challenge in many manufacturing facilities. Companies are therefore seeking new technologies that can reduce risks at the workplace. By making the workplace safer, companies will significantly reduce the costs associated with workplace injuries.
The National Safety Council approximates that 4,500,000 injuries occur in the workplace every year. This article will discuss the latest technologies that can help improve safety in manufacturing facilities and warehouses.
5 Tech Upgrades to Increase Safety
1. Internet of Things (IoT)
Internet of Things (IoT) refers to a system of physical objects integrated with software, sensors, and other technologies. IoT aims to connect and exchange data with other systems and devices over the internet without human intervention.
Industrial manufacturing and warehousing are using IoT to collect and analyze data. This data is critical in improving safety on the warehouse and manufacturing floor. The data is used to predict trends of workers and identify risks that could cause injury. The technology can quickly locate workers and notify them of hazardous situations.
IoT can also monitor equipment and vehicle navigation within a warehouse, hence it can prevent a collision. The technology also identifies protruding objects that could result in a collision.
Predictive analysis is also another crucial role of IoT in safety enhancement. Real-time IoT data is integrated with artificial integrity and advanced analytics to establish key performance trends. Variances can then be detected as soon as they appear, preventing potentially dangerous situations like overheating or gas leaks.
However, there are cyber security concerns when implementing IoT. Therefore, manufacturers should look closely at IoT devices and partners to ensure that they are implemented and maintained properly.
2. Additive Manufacturing and 3D Printing
Additive manufacturing (AM), commonly known as 3D printing, is an industrial production approach, which enables more robust, lighter parts and systems to be created. The move from analog to digital has made this technological advancement a possibility.
AM has brought about safety, flexibility, and efficiency to industrial processes. AM uses 3D object scanners and computer-aided design (CAD) to instruct the hardware to arrange materials in precise geometrical shapes.
Additive manufacturing creates objects by adding materials. Creating objects using traditional techniques often requires removing material through carving, machining, shaping, and milling.
3D printing and rapid prototyping are usually used to refer to additive manufacturing. However, they are subsets of AM. AM has notably led to new software advances and materials, which have cleared paths for new cost-effective applications.
Bioprinting and digital autonomy have allowed for seamless switching between different materials. Furthermore, this technology has enabled manufacturers to visualize the potential for mass customization better.
3. Advanced Automation and Robotics
Manufacturing and warehousing facilities have seen a continued trend towards collaborative environments. Smart manufacturing has enhanced safety and efficiency by using autonomous mobile robots (AMRs) and automated guided vehicles (AGVs).
Autonomous mobile robots (AMRs) use advanced navigation technology to study the entire facility and create a map. AMRs are then able to determine the most effective route without the intervention of a human being. In addition, this advanced navigation technology allows AMRs to move around obstacles without the need for human intervention.
However, AMRs are not ideal for transporting all types of materials within your facility. A robot that chooses a different route every time could be less effective. In addition, a robot that can change its course, especially when carrying heavy materials, can be a concern.
Automated guided vehicles (AGVs) follow a specific route to transport materials in a facility. These routes are integrated onto the facility's floor, and the AGV uses wires or magnets laid on the floor. An automatic guided vehicle system is ideal for heavy materials. However, AGVs cannot move around obstacles and cannot determine their own routes. They are therefore less flexible than AMRs.
4. Working with Wearables
Manufacturing facilities and warehouses can use wearables to monitor environmental conditions and workers' health analytics. Wearables enable workers to understand their health. In addition, companies can monitor the health and safety of workers, especially those working in hazardous conditions.
Wearables such as smartwatches, jackets, and helmets are integrated with sensors. These wearables can measure key personal health indicators such as blood oxygen levels, temperature, and heartbeat.
Supervisors can use such data to identify workers showing signs of fatigue, stress, or strain. The supervisors can then take preventive action. Such wearables have proven to be effective in enhancing employee safety and productivity.
Wearables can also facilitate hands-free training in a manufacturing setup. Hands-free training is critical since inexperience can lead to severe injuries, poor performance, and equipment damage.
Manufacturing and warehousing facilities can also use wearables to enhance situational awareness. Modern warehousing and manufacturing facilities are dynamic. The facility's settings are constantly changing to allow for more work. It is challenging for workers to remain aware of shelving, equipment, and hardware that keeps moving. Wearables can frequently update workers on what is going on around them.
5. 5G Network
Manufacturing and warehousing facilities are moving towards advanced technology, which calls for reliable internet connectivity. Internet of things, many connected devices, and bandwidth demands have intensified due to the growth of technologies adopted by industries.
5G network technology satisfies the need for secure, reliable, and high-speed connectivity. 5G network can reach speeds of 10 gigabits per second, approximately 100 times faster than 4G.
Despite this, there are significant concerns about the risk of losing connectivity in warehouses and manufacturing facilities. With a lot of devices depending on internet connectivity, a sudden loss of connection could be devastating.
For example, a collaborative robot transporting materials suddenly losses connection. Though a built-in software could provide some mitigation, prolonged loss of connection could result in significant negative consequences.
Conclusion
The need to enhance safety in manufacturing and warehousing facilities has called for more advanced technologies. Many industries are adopting these technologies to ensure that they comply with safety standards and regulations.
In addition, many warehousing and manufacturing facilities seek to reduce costs associated with workspace injuries. However, not all tech upgrades are ideal for all manufacturing and warehousing facilities. It is critical to undertake an assessment and determine which technology is suitable for your facility.
Luke Goodwin is an experienced content marketing manager with a demonstrated history of working in the logistics and supply chain industry. Currently, he works at FlexQube where he creates valuable content relevant to the intralogistics and material handling industries. To learn more about FlexQube and see more articles from the industry you can visit their news website.
Guest Post
New York Engineers always welcome guest posts that are relevant and informative.
Join 15,000+ Fellow Architects and Contractors
Get expert engineering tips straight to your inbox. Subscribe to the NY Engineers Blog below.