Backflow Prevention Systems
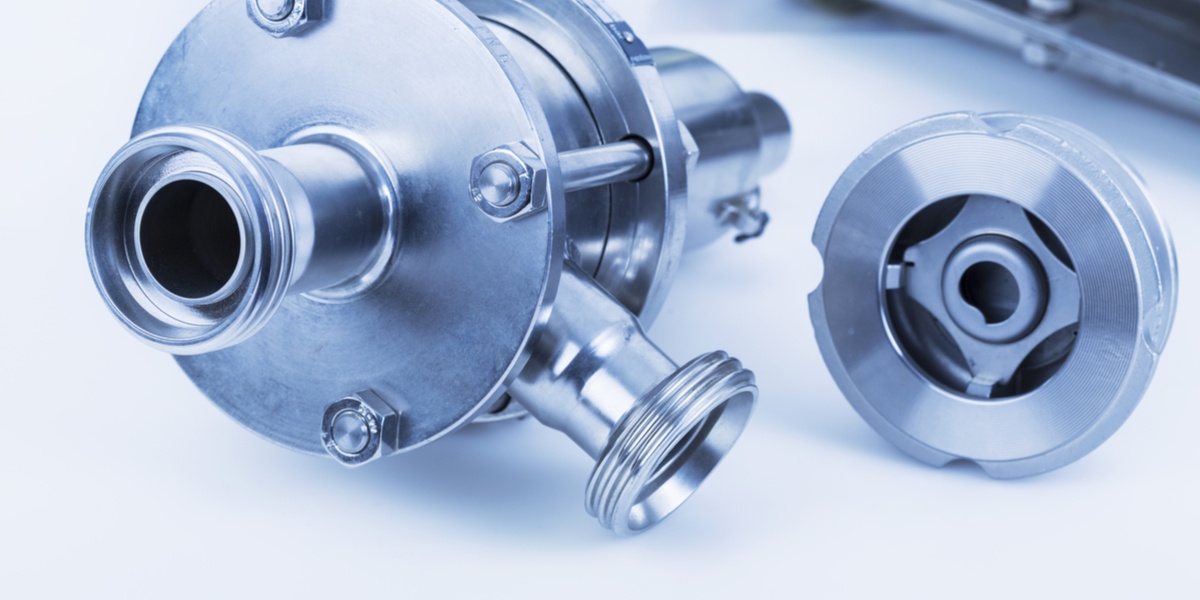
Water distribution systems are designed to make water flow in a specified direction: from the source to the consumer, and then from the consumer to the sewage system. However, some operating conditions can cause a pressure difference opposite to the intended flow direction, causing backflow when the system lacks protection measures. The main risk associated with backflow is contamination of the potable water supply with harmful substances.
What Causes Backflow?
For backflow to occur, there must be a pressure change that pushes water opposite to the normal flow direction. These pressure changes can be induced by gravity, vacuum formation and other physical effects. Based on how the reverse pressure difference is established, the causes of backflow can be divided into back siphonage and back pressure.
BACKFLOW CAUSE |
DESCRIPTION |
Back siphonage |
Can occur when pressure is lowered upstream from the point of use. Some common locations for back siphonage are tanks and water troughs, especially when water pressure drops below atmospheric pressure. Back siphonage can be caused by undersized or broken pipes, and by sudden peaks in water demand. |
Back pressure |
Can occur when pressure is raised downstream by a system that uses water. Back pressure is common in the piping of multi-story buildings due to the effect of gravity, and can also be induced by the high static pressure in fire protection systems. Other causes of back pressure include pumping and water expansion with high temperature. |
Although the physical process is different for back siphonage and back pressure, the final result is the same: water tends to flow backward due to the reverse pressure, and it can carry pollutants upstream.
Make sure your water supply is protected from backflow.
The Role of Cross-Connections
A cross-connection can be defined as any existing or potential connection between a potable water supply and a pipe or device that holds a non-potable fluid, including the water itself after use. The definition applies even when the non-potable fluid is only present occasionally. Note that fluids may be considered non-potable due their own composition, or due to solid particles and gas mixed with the fluid. The following are some examples of systems that create cross-connections:
- Automatic fire sprinkler systems
- Irrigation systems
- Beverage production equipment
- Dialysis equipment
There are also cases where a cross connection is created accidentally. Assume a hose is used to fill a swimming pool: when the hose is suspended above the pool, there is no cross connection; however, one is created if the hose is submerged, since water can flow in once the pressure is gone.
Eliminating cross connections is not possible because they are fundamental for equipment that requires pressurized water. Therefore, protection measures must be deployed to prevent backflow and potential contamination of the potable water supply.
Classification of Backflow Preventers
Backflow preventers can be classified based on physical construction, application or type of installation. The main types of backflow prevention assemblies are listed below, and each type has a dedicated standard from the American Society of Safety Engineers (ASSE).
DEVICE |
APPLICABLE STANDARD |
Reduced Pressure Backflow Assembly |
ASSE 1013 |
Double Check Valve Assembly |
ASSE 1015 |
Pressure Vacuum Breaker |
ASSE 1020 |
Reduced Pressure Detector Assembly |
ASSE 1047 |
Reduced Pressure Detector Assembly Type II |
ASSE 1047 |
Double Check Detector Assembly |
ASSE 1048 |
Double Check Detector Assembly Type II |
ASSE 1048 |
Spill Resistant Vacuum Breaker |
ASSE 1056 |
Each type of backflow prevention assembly has different operating features, which means not all of them may be suitable for a specific application. Before specifying a device, it is important to make sure it matches the application requirements.
Application Requirements
Backflow prevention devices are used in many applications and industries, each with different performance requirements: fire protection systems, agriculture, waterworks, etc. The backflow preventers in these systems must be suitable for the flow conditions encountered:
- Water flow is constant in waterworks and plumbing applications.
- Irrigation systems only operate around 2% of the time and are static the remaining 98%.
- Fire protection systems are permanently on standby, but must sustain a specified static pressure to respond effectively when needed.
Installation Requirements
In addition to being classified by device and application, backflow prevention systems also differ in how they are installed. Their location can be outdoors, indoors or below grade, and their orientation can be horizontal or vertical. Each configuration comes with specific challenges:
LOCATION |
MAIN ISSUES TO CONSIDER |
Outdoor |
Soil erosion and freezing temperatures, and human factors like vandalism and theft. Requires a protective enclosure in most cases. |
Indoor |
Preventing water discharge. |
Below grade |
Not all backflow preventers are suitable, and the installation must be accessible for testing, maintenance and reparation. |
Vertical |
Not all backflow preventers are suitable. For this reason, horizontal installations are more common. |
In applications that require an uninterrupted water supply, multiple connections or manifold assemblies may be needed - this includes some industrial applications, as well as hospitals and resorts.
Federal Considerations for Backflow Prevention Devices
The Safe Drinking Water Act (SDWA) was approved by the US Congress in 1974. The SDWA makes the water supplier responsible for quality at the source, meeting the standard established by the US Environmental Protection Agency. However, once the water has been delivered, the customer is responsible for preventing its contamination with backflow.
The SDWA was updated in 2014, requiring all plumbing fixtures to be manufactured with less than 0.25% leaded brass content - this includes backflow prevention devices.
Conclusion
Although the SDWA ensures water suppliers provide quality, backflow from customer equipment can cause contamination if ignored. Make sure your installation is equipped with backflow prevention devices, properly selected for their intended applications. By working with qualified plumbing design professionals, you can ensure this requirement is covered while meeting any building codes that apply.
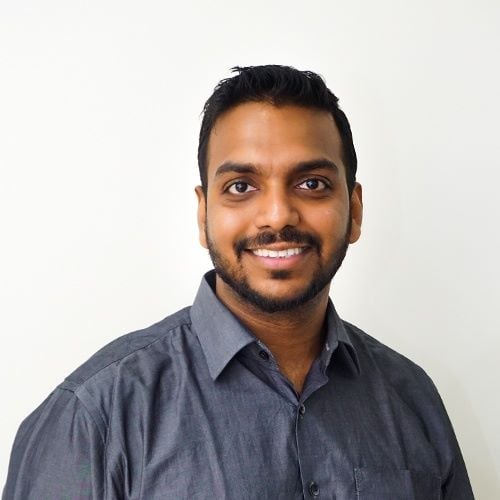
Anuj Srivastava
Anuj Srivastava is a principal partner at NY Engineers. He is known for his MEP franchise market knowledge. Anuj is currently leading a team of 100+ MEP/FP engineers and has successfully led over 1500 franchise projects in the US.
Join 15,000+ Fellow Architects and Contractors
Get expert engineering tips straight to your inbox. Subscribe to the NY Engineers Blog below.