Common Insulation Materials Used in Buildings
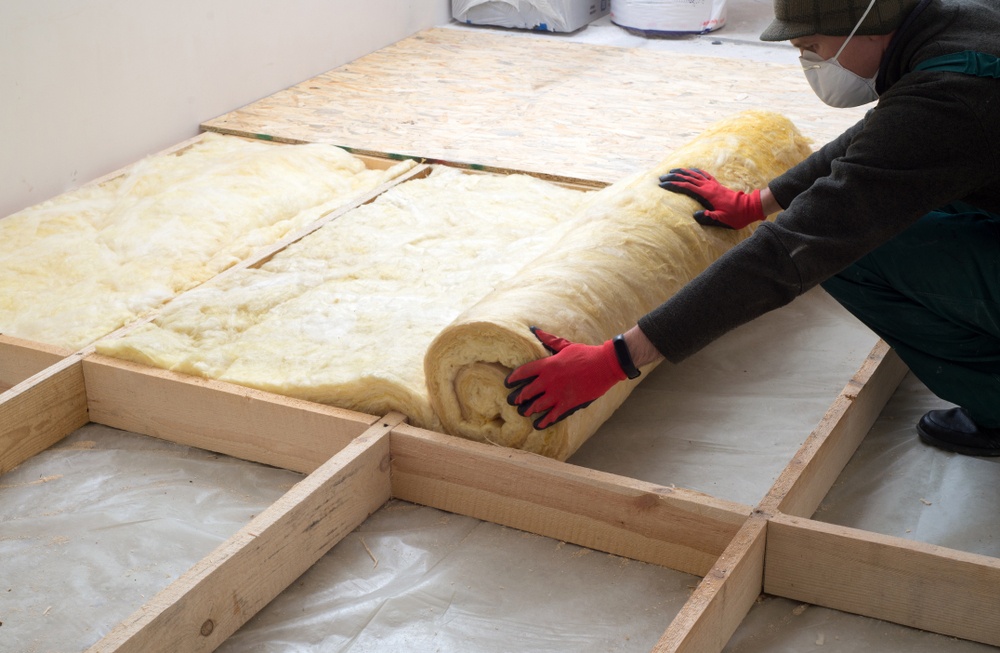
Insulation materials come from different sources like minerals, vegetable fibers, animal products, and synthetic compounds. Like in many engineering decisions, each material has advantages and disadvantages that must be considered when selecting insulation for buildings.
This article provides an overview of the main options in the market, and how they perform in actual projects. There are insulation materials that are no longer used, but may be found in older constructions - one example is insulation with an asbestos content, which has been outlawed.
Make sure your building has the right insulation and reduce your energy costs.
Fiberglass
Fiberglass is one of the most popular insulation materials, made by weaving fine strands of glass. It is manufactured mostly from recycled glass.
Characteristics:
-Minimizes heat transfer
-Non-flammable
-R-values range from R-2.9 to R-3.8 per inch
-Low cost
-Environmentally friendly
-Does not absorb water
-Can be dangerous for installers, requiring special protection equipment.The small particles of glass can damage the eyes, lungs and skin.
-Loose-fill insulation is applied using an insulation-blowing machine
Available in:
-Blankets (batts and rolls): fiberglass batt can be found as medium or high-density, with higher R-values than standard batts
-Loose-fill and blown-in
-Blow-in Blanket System (BIBS): a variation of loose-fill insulation that is blown dry, and tests have proven a higher insulation level than other types of fiberglass
-Rigid boards
-Duct insulation
-Rigid fibrous insulation
Mineral Wool
Mineral wool refers to two types of insulation material:
- Rock wool, made from basalt or diabase
- Slag wool, made from blast furnace slag from steel mills
Characteristics:
-Contains an average of 75% post-industrial recycled content
-Does not need additives to make it fire resistant
-Not recommended in extreme heat environments
-Non flammable
-R-value ranging from R-2.8 to R-3.5
-Environmentally friendly
-Does not melt and is not combustible
-Moderate cost
Available in:
-Blanket (batts and rolls)
-Loose-fill and blown-in
-Rigid fibrous or fiber insulation
Cellulose
Cellulose is made from recycled paper products, mainly newspapers. During the manufacturing process, paper is first broken down into smaller pieces and then fiberized. Cellulose is one of the most eco-friendly forms of insulation, and is available in loose-fill and blown-in versions.
Characteristics:
-Environmentally friendly
-Most of its content is recycled (82-85%)
-Inhibits airflow
-Mineral borate is added to ensure fire and insect resistance
-Requires no moisture barrier
-R-values range from R-3.1 to R-3.7
-Excellent product for minimizing fire damage
-Due to its compactness, it contains almos not oxygen within
-Can generate allergies
-Requires skilled workers for installation
-Moderate cost
Polystyrene
Polystyrene is a colorless and transparent thermoplastic. Polystyrene insulation is available in many versions:
- Molded expanded polystyrene (MEPS), commonly used in foam boards and as small foam beads.
- Expanded polystyrene (EPS), made of small plastic beads fused together
- Extruded polystyrene (XPS), is a molten material that is pressed into sheets, also known as styrofoam
Characteristics:
-Low cost, but not environmentally friendly
-Flammable, needs to be coated with a fireproof chemical
-Lightweight
-Tends to accumulate static electricity
-Can be difficult to control
-Thermal drift or ageing occurs over time-R-value depends on density: expensive XEP has an R-value of R-5.5, while EPS offers R-4
-Waterproof
-Excellent sound and temperature insulation
-Smooth surface
Available in:
-Loose fill (small beads)
-Concrete block insulation and insulating concrete blocks
-Insulating concrete forms (ICF)
-Structural insulating panels (SIP)
-Foam board or rigid foam
Polyurethane
Polyurethane is available in closed-cell foam and open-cell foam. Closed-cell foams possess high-density cells filled with a gas (non-HCFC), which allows the foam to expand. Open-cell foams are not as dense and are filled with air, producing a spongy texture when applied. However, some low-density varieties use carbon dioxide as the foaming agent.
Characteristics:
-High cost
-Not environmentally friendly
-Fire resistant
-Great sound insulator
-New foams use non-CFCs gas as a blowing agent
-Lightweight
-R-value of R-6.3 per inch
-Contains low-conductivity gas in its cells
-Thermal drift or ageing occurs only in closed-cell foams in the first two years after application. To slow down thermal drift, a layer of foil and plastic facings can be applied facing the open aire space creating a radiant barrier.
-Sprayed foam is cheaper than foam boards and performs better.-Sprayed foams can expand rapidly or slowly depending on the user demands
-Resistant to water vapor diffusion
Available in:
-Foam board or rigid foam
-Sprayed foam and foamed-in-place
-Structural insulated panels (SIP)
Natural Fibers
Many natural fibers have applications in building insulation. Some examples are cotton, sheep’s wool, straw and hemp.
Cotton is available in batts and rolls, and it offers the following features:
- Consists of 85% recycled cotton and 15% plastic fibers
- Treated with borate (flame retardant and insect repellent)
- Minimum energy requirements for manufacturing
Sheep wool is also available and batts and rolls, and it has the following characteristics:
- Treated with borate to resist pest, fire and mold.
- Holds water, but repeated wetting and drying reduces borate effect
Straw has been used as insulation since the 1930s. It is available as boards or structural insulated panels (SIP), which are sound-absorbing and with typical width of 2" to 4".
Hemp is not a common insulation material in the US, although it has R-values comparable to those of other fibrous insulation types.
Polyisocyanurate
Polyisocyanurate or polyiso is a closed cell thermoset plastic similar to polyurethane. It contains a low-conductivity HCF-free gas and can be foamed in place, which is cheaper and more efficient than using foam boards.
Polyiso experiences thermal drift or ageing in the first 2 years after manufacturing, but foil and plastic facings can be applied facing the open air space. This works as a radiant barrier, stabilizing the R-value
Polyiso is available in the following forms:
- Foam board or rigid foam
- Sprayed foam and foamed-in-place
- Laminated insulation panels
- Structural insulated panels (SIPs)
Cementitious Foam
As implied by its name, this insulation material is cement-based. It is nontoxic and nonflammable, and made from minerals extracted from seawater. Cementitious foam is similar to polyurethane foam, and can be sprayed and foamed-in-place.
Phenolic Foam
Phenolic foam is another type of insulation that is sprayed and foamed-in-place. It uses air as a foaming agent, and can shrink up to 2% after curing.
What Are Insulation Facings?
Facings are coatings attached to insulation during the manufacturing process or afterwards. Their main purposes are protecting the surface, holding the insulation together, and simplifying the attachment to building components. Depending on the type of facing, it can also accomplish the following functions:
- Acting as an air and vapor barrier
- Flame resistance
- Aluminum foil in particular is also a radiant barrier
Some most common types of facing are kraft paper, white vinyl sheeting and aluminum foil.
Insulation Materials That Are No Longer Used
Some insulation materials that were used in the past are now outlawed, unavailable or not used due to health issues. Some examples are vermiculite, perlite and urea-formaldehyde.
Vermiculite and perlite were used to insulate attics before the 1950, but are not used anymore because they contain asbestos. These insulation materials were mostly available as loose-fill or pellets.
- Certified contractors in handling asbestos are required for removal from existing buildings
- Were applied by heating rock pellets until they popped
- Allowed mixing with cement
Urea-formaldehyde is a sprayed foam that was commonly used in the 1970s and 1980s. However, due to improper installations, many health-related court cases took place. As a result, urea-formaldehyde was prohibited in residential buildings, but is still used for masonry walls in commercial and industrial buildings.
- Uses compressed air as the foaming agent
- Does not expand as it cures
- Nitrogen- based UF takes longer to cure
- Water vapor can pass through
- Does not contain a fire retardant
Conclusion
The sheer number of insulation materials available may seem overwhelming. However, with professional engineering services, you can make sure that your project has optimal insulation. A well-insulated building has lower heating and cooling expenses, since effective insulation minimizes heat gain during summer and heat loss during winter.
When effective insulation is combined with high-efficiency HVAC design, your building achieves a drastic reduction of heating and cooling costs. Applying insulation is cheaper and simpler in new buildings, since there is no need to disturb an existing construction. Developers who are planning a new project should keep this in mind.
Nearby EngineersNew York Engineers has a MEP design track record of 1,000+ projects. Contact us via email (info@ny-engineers.com) or phone (786) 788-0295212-575-5300, and make sure your building systems meet codes.
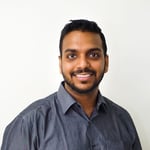
Anuj Srivastava
Anuj Srivastava is a principal partner at NY Engineers. He is known for his MEP franchise market knowledge. Anuj is currently leading a team of 100+ MEP/FP engineers and has successfully led over 1500 franchise projects in the US.
Join 15,000+ Fellow Architects and Contractors
Get expert engineering tips straight to your inbox. Subscribe to the NY Engineers Blog below.