How to Calculate Labor Cost in Construction
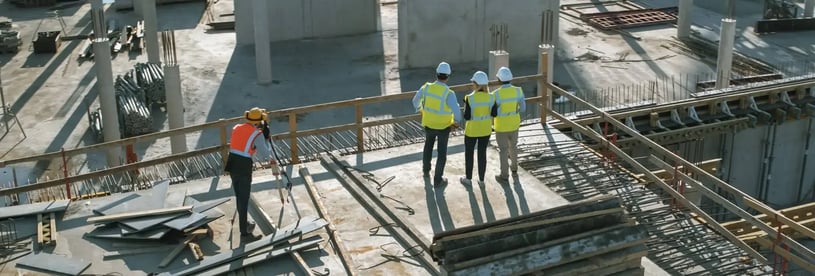
Calculating labor costs in construction is a crucial skill that ensures a project's financial success. To determine labor costs, you must consider the hourly wage, labor burden, and hours worked or needed. This means factoring in variables such as workers' compensation, payroll taxes, and benefits to understand the true cost of employing each worker.
Understanding these elements is essential for accurate budgeting and resource allocation. Effective calculation methods, like using the hourly wage and labor burden formula, provide clarity on how labor expenses impact the overall project budget. Costs typically account for a significant portion of construction expenses, often making up 40-50% of total project costs, according to the rule of two method.
Mastering these calculations empowers construction managers to make informed decisions about pricing, bids, and resource management. Utilizing tools like a labor cost calculator can streamline this process, offering a straightforward approach to managing project costs efficiently.
Understanding Labor Cost in Construction
Labor costs in construction include various expenses beyond just wages. The experts at this website remind us that they encompass benefits, taxes, and training, all of which significantly impact a project's budget and financial success.
Components of Labor Cost
Construction labor costs are complex, composed of multiple elements that contribute to a project’s total expenses. Salaries and wages form the bulk of these costs. Benefits such as health insurance, retirement contributions, and paid leave also play a crucial role.
Additionally, there are indirect costs like training expenses and onboarding efforts, which ensure that the workforce remains efficient and skilled. Other factors include payroll taxes required by law.
Understanding these components aids in more accurate budget planning, ensuring that projects remain financially viable and successful. Accurate estimation minimizes surprises and facilitates smoother project execution.
Factors Influencing Labor Cost
Several factors influence labor costs in construction, impacting how these expenses are managed. Geographic location can play a significant role, as labor rates vary widely between regions. Economic conditions can also drive fluctuations in demand for skilled workers, thereby affecting wages.
Project complexity and required skill levels also impact costs. Highly specialized tasks may necessitate higher wages due to the expertise required. Additionally, employment laws and regulations influence labor costs through mandated standards and minimum wages.
Technology adoption can potentially reduce labor costs by enhancing efficiency, though initial investments may be required. Managing these factors proactively can help maintain project budgets within acceptable limits.
Calculating Labor Cost
Calculating labor costs in construction involves determining wage rates, estimating hours worked, and incorporating additional expenses. This ensures accurate project budgeting and resource allocation.
Determining the Wage Rates
A crucial first step is identifying the wage rates for different types of labor involved. Wage rates include the base pay for each worker, alongside any benefits and legally required overheads like social security and unemployment taxes. It helps to maintain a detailed list of these costs.
Contractors often account for varying skill levels and specialties. Using data from resources like the Department of Labor ensures that rates comply with current standards. This approach can prevent budget overruns and improve project profitability.
Estimating the Hours Worked
Estimating the total hours required is another vital element. Contractors must consider the project's scope, working conditions, and team efficiency. They usually leverage past project data to predict labor needs accurately.
Various methods exist such as the rule of two, which helps forecast labor expenses by multiplying known costs. This method, combined with historical data, offers a clearer picture of probable hours. Modern project management software can also track and predict labor hours, enhancing planning efficiency.
Incorporating Additional Expenses
Additional expenses beyond hourly wages contribute significantly to labor costs. These may include insurance, equipment use, and worker transportation. Contingencies like delays or accidents also need consideration.
Incorporating a contingency budget, often around 10% of direct labor costs, ensures that unexpected expenses don’t disrupt the project. This contingency reflects the dynamic nature of construction projects and provides a financial buffer. Calculating labor costs extends beyond wages, so a comprehensive approach enriches the budgeting process.
Labor Cost Analysis
Conducting a thorough labor cost analysis involves understanding key aspects such as productivity levels and industry benchmarks. These elements help to accurately evaluate and manage labor expenses in construction projects.
Assessing Labor Productivity
Labor productivity in construction measures the output relative to the input, often quantified as the amount of work completed per hour. Analyzing productivity requires monitoring work rates, identifying delays, and assessing the skills of the workforce.
Key Metrics:
- Units produced per labor hour
- Number of completed tasks
- Time delays encountered
By collecting data on these metrics, companies can spot inefficiencies and implement targeted improvements. For instance, outdated tools or processes might hinder productivity. Companies can employ techniques like regular training or upgraded equipment to leverage labor efficiency effectively.
Benchmarking Against Industry Standards
Benchmarking involves comparing a company's labor costs and productivity levels with industry averages. This offers valuable insights into how well a company is performing relative to its competitors.
Steps to Benchmarking:
- Gather Data: Collect data on average wages, overtime expenses, and benefit costs.
- Analyze Trends: Compare with similar firms to identify disparities.
- Implement Changes: Use discrepancies to drive changes, such as optimizing workforce allocation.
Having a robust benchmarking process allows construction firms to align their labor costs and productivity with industry standards, enhancing competitiveness and profitability. For deeper insights into managing these aspects, resources such as this construction labor costs guide can be invaluable.
Optimizing Labor CostOptimizing Labor Cost
Optimizing labor costs in construction involves implementing efficient practices and leveraging technological advancements to boost productivity. Companies can enhance profitability and project efficiency by adopting these strategies.
Implementing Efficient Practices
Efficient practices begin with clear communication and thorough planning. Establishing detailed schedules and breaking tasks into manageable parts can prevent delays. Regular training ensures the workforce is skilled and versatile. Cross-training employees allows them to adapt to various tasks, reducing downtime and improving overall productivity.
Monitoring worker performance through regular evaluations helps identify areas for improvement. Project managers can also use lean construction practices to minimize waste and unproductive time. Setting performance benchmarks and providing incentives motivates workers to maintain high standards. Efficient practices contribute significantly to cost optimization.
Leveraging Technology for Productivity
Technology plays a vital role in optimizing labor costs. Utilizing project management software simplifies scheduling and task management. Tools like BIM (Building Information Modeling) enable project managers to visualize the construction process, identifying potential issues before they arise.
Drones and robotics automate repetitive tasks, reducing manual labor requirements. These technologies improve safety and efficiency on-site. Wearable technology monitors worker health and safety, contributing to reduced downtime and enhanced productivity.
Implementing construction management apps on mobile devices ensures real-time updates and communication among team members. This integration of technology leads to a more cohesive workflow, minimizing delays and rework. Monitoring technology advancements and adopting suitable solutions are essential steps in optimizing labor costs effectively.
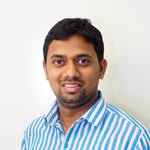
Ravindra Ambegaonkar
Ravindra, the Marketing Manager at NY Engineers, holds an MBA from Staffordshire University and has helped us grow as a leading MEP engineering firm in the USA
Join 15,000+ Fellow Architects and Contractors
Get expert engineering tips straight to your inbox. Subscribe to the NY Engineers Blog below.