How To Design Warehouses For Small Businesses In 2023?
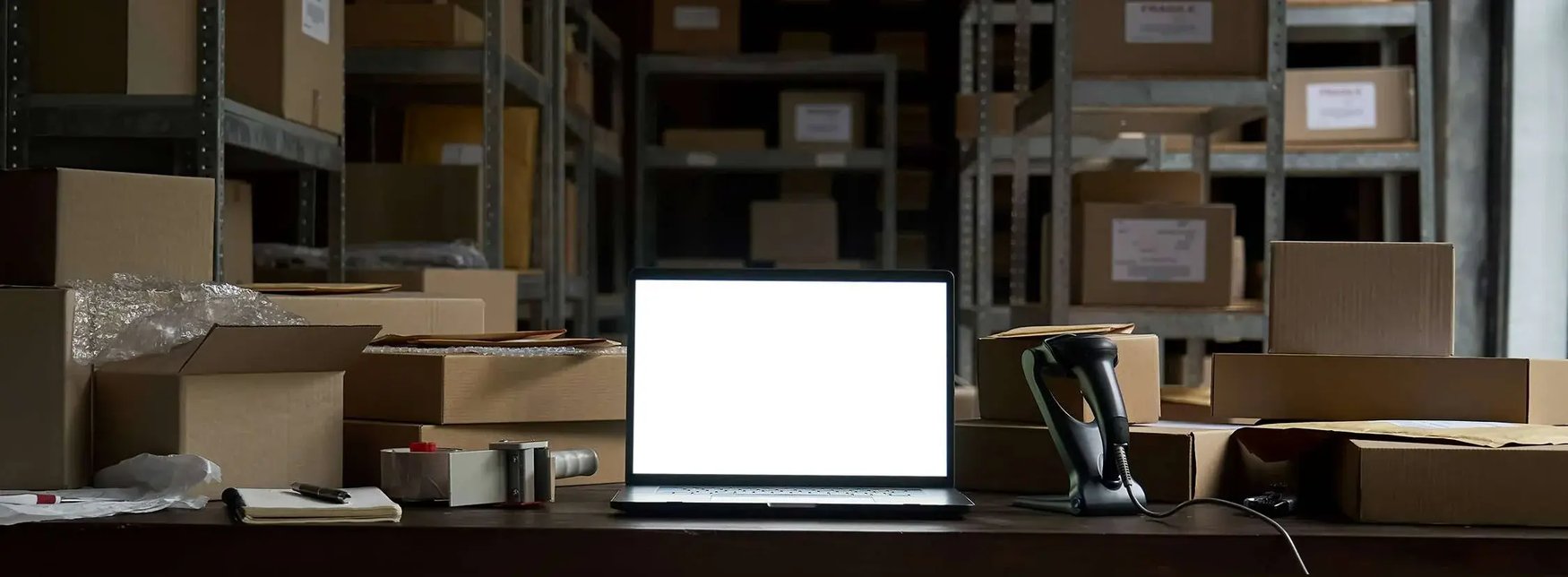
In the intensely competitive business landscapes of today, small businesses have to go head to head with large, well-capitalized businesses. One key area where these disparities are fairly evident, involves storage and warehousing spaces.
With rising rents, long-term commitments, and added overheads, small businesses are already at a significant disadvantage. However, by adopting certain smart strategies, and a warehouse designed to enhance productivity and streamline operations, small businesses can still gain an upper hand in 2023, with the rise of micro-fulfillment and same-day deliveries in recent years.
In this article, we cover some tried-and-tested approaches in this regard, particularly tailored towards small businesses with limited resources and capital to get started with.
Assessing Space & Resource Constraints
Before embarking on the design process, small businesses must thoroughly assess their space and resource constraints. Understanding the available square footage, ceiling height, budget, and staffing limitations is crucial for creating an effective warehouse layout.
Additionally, identifying specific business requirements and operational workflows will help determine the most suitable design approach.
Cost considerations must be a part of this assessment, with the overheads incurred by a warehouse directly absorbed into the cost of goods sold during the period in question. This helps make better decisions, particularly in regards to the type of warehouse to invest in, and the equipment to buy.
Efficient Warehouse Layouts
Efficiency is a key factor in designing warehouse layouts for small businesses. An efficient layout ensures that operations run smoothly, reducing the time and effort required for picking, packing, and shipping tasks.
Here are some important considerations when designing an efficient warehouse layout:
U-Shaped Layout: One popular layout for small businesses is the "U-shaped" layout. This layout places the receiving, storage, and shipping areas in a U-shaped configuration.
This design minimizes travel distance for employees, as they can move continuously from receiving to storage and shipping without unnecessary detours.
Zoned Layout: This layout divides the warehouse into distinct zones based on product type, order frequency, or other relevant criteria.
Each zone is dedicated to specific products or operations, allowing for streamlined processes and reducing the need for extensive travel across the warehouse. This zoning approach helps in improving organization and expediting order fulfillment.
Clear Pathways & Signage: In an efficient warehouse layout, clear pathways are crucial to ensure the smooth movement of personnel and equipment.
Wide aisles and designated walkways should be incorporated, allowing for easy access and reducing the chances of collisions or congestion. Additionally, clear signage throughout the warehouse helps guide employees and ensure accurate and timely product retrieval.
Optimized Product Placement: Strategic product placement is essential for efficient warehouse operations. Fast-moving or high-demand items should be placed near the shipping area for quick access, reducing picking time.
Similarly, frequently restocked items should be located near the receiving area to minimize the distance traveled during replenishment. Analyzing product velocity and incorporating it into the layout design can significantly improve overall efficiency.
Cross-Docking Area: Incorporating a cross-docking area can be beneficial for small businesses involved in quick turnaround operations.
Cross-docking involves transferring goods directly from inbound to outbound shipments, bypassing long-term storage. This eliminates the need for storage space, reduces handling costs, and expedites order fulfillment.
Utilization of Vertical Space: Small businesses often have limited floor space, making it crucial to maximize vertical space.
Vertical storage solutions, such as tall shelving units or mezzanines, enable efficient use of available space. By expanding upward, businesses can store more inventory without expanding the warehouse's footprint.
Flexibility For Growth: Designing an efficient warehouse layout should also account for future growth. Modular or adjustable storage solutions, such as movable racks or shelving systems, allow for easy reconfiguration as the business expands.
This flexibility ensures that the warehouse layout can adapt to changing needs and accommodate increased inventory levels.
Small businesses can create an efficient and organized environment by considering these factors and tailoring the warehouse layout to specific business requirements.
An optimized warehouse layout minimizes unnecessary movement, reduces labor costs, and enhances productivity, ultimately improving customer satisfaction and business success. However, as discussed above, this has to be done in-consideration with business requirements.
For example, a business that deals with low volume, light weight products would do well to do away with extensive equipment investments, instead hiring just laborers. With higher volumes, however, it makes sense to invest in infrastructure, given the low marginal cost of each unit.
Maximizing Storage Capacity With Rack Systems
Rack systems play a pivotal role in maximizing storage capacity within limited space. Depending on their specific needs, small businesses can leverage various rack types, such as selective, push-back, or drive-in racks.
Selective racks offer flexibility for fast-moving items, while push-back or drive-in racks provide high-density storage. Customized rack solutions can help optimize space utilization, ensuring efficient inventory organization and retrieval.
Overall, rack systems make effective warehousing an option for small and medium-sized businesses, which otherwise would not have the capital required for other alternatives.
Used Containers & Storage Racks
Used containers and storage racks offer small businesses affordable and versatile storage solutions. Containers such as pallet containers or plastic bins, can be stacked or organized on racks, allowing for efficient use of vertical space.
Here's a detailed explanation of how small businesses can benefit from using previously owned containers for versatile storage.
1. Versatile Storage Options: Used containers and storage racks provide small businesses with versatile storage options that accommodate various types of inventory.
Containers such as pallet containers or plastic bins offer a flexible and scalable solution for storing different sizes and shapes of products. These containers can be stacked or organized on storage racks, maximizing vertical space utilization within the warehouse.
2. Cost-Effective Solution: Purchasing new containers and storage racks can be expensive, especially for small businesses with limited budgets. Opting for used containers and storage racks offers a cost-effective alternative.
Used containers are often available at a fraction of the cost of new ones, allowing businesses to allocate their resources more efficiently. Small businesses can invest in other areas of their operations by saving on storage equipment costs.
3. Durable & Reliable: Despite being used, containers and storage racks are typically constructed to withstand the rigors of industrial environments.
They are designed to be durable and reliable, providing secure storage for inventory. These used storage solutions have proven their functionality and durability in previous applications, making them a reliable choice for small businesses.
4. Environmental Sustainability: Using previously-owned containers and storage racks aligns with environmental sustainability goals. By reusing existing storage equipment, small businesses contribute to reducing waste and minimizing their carbon footprint.
Embracing sustainable practices, even at the warehouse level, showcases a commitment to environmental responsibility.
5. Availability & Quick Implementation: Used containers and storage racks are readily available, making them a convenient option for small businesses requiring immediate storage solutions.
Businesses can quickly source used equipment, allowing for swift implementation and minimal disruption to warehouse operations.
Embracing Sustainable Warehouse Design
In an increasingly environmentally conscious world, small businesses should consider incorporating sustainable practices into their warehouse design
Energy-efficient lighting systems, such as LED lights, can reduce electricity consumption, and are a great way to get started.
Implementing insulation and efficient HVAC systems can help regulate temperature and minimize energy waste. Additionally, adopting recycling programs for packaging materials and utilizing eco-friendly storage solutions, such as reusable containers, contribute to sustainable warehouse operations.
Final Thought
Designing an efficient warehouse for small businesses in 2023 requires careful consideration of space limitations, available resources, and specific operational needs. With strategic planning and innovative solutions, small businesses can create warehouses that support their growth and success in a competitive marketplace.
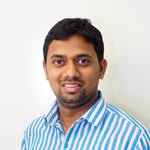
Ravindra Ambegaonkar
Ravindra, the Marketing Manager at NY Engineers, holds an MBA from Staffordshire University and has helped us grow as a leading MEP engineering firm in the USA
Join 15,000+ Fellow Architects and Contractors
Get expert engineering tips straight to your inbox. Subscribe to the NY Engineers Blog below.