How to Select a Contractor
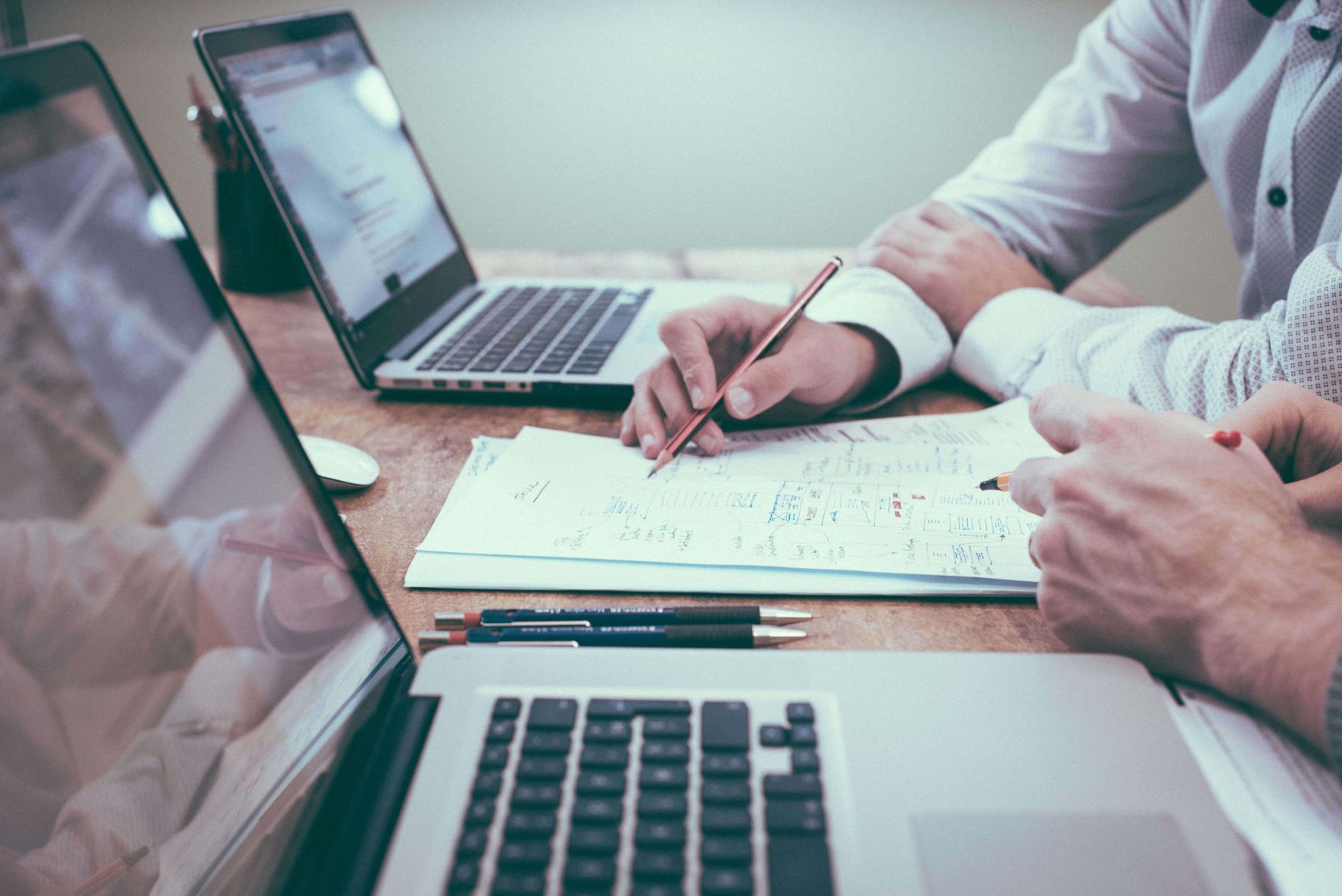
Tips for Effective Contractor Selection in Engineering Projects
One of the key elements that determines project success is selecting the right contractor for the job. Although it may be tempting to focus on minimizing cost, a better approach is to maximize value and optimize cost. After all, an engineering project is an investment; the best offer is not always the one with the lowest price, but the one that offers the highest return on each dollar spent.
Effective communication is key during the bidding process: if the participating contractors understand the project requirements clearly, they can craft their proposals accordingly. Without proper specifications, even the most qualified contractors may struggle to provide a suitable offer. Effective communication is so important for project success, that the Project Management Institute dedicates a whole chapter of its Body of Knowledge to the topic.
Before proceeding with a bidding process, hiring an engineering consulting or supervision firm is highly recommended. They can help you expedite the process, while providing technical guidance and managing correspondence with contractors. Even with a clearly defined project scope, it is normal for contractors to request additional information or clarifications.
Bid Leveling: Setting a Common Ground for Comparison
Project bids can only be compared with each other if the contractors are quoting the same scope of products and services. When sending a Request for Proposals (RFP), include a scope document that breaks down the work into specific items, and where each item is priced individually. This allows bids to be compared side by side, something not possible when each contractor provides a different breakdown of the project work.
Creating a detailed project scope consumes extra time at the beginning but saves much more time later in the process. Since bids can be directly compared to each other, communication becomes more effective during the contractor selection process, reducing the number of clarifications and requested corrections.
The Project Management Institute (PMI) recommends using a Work Breakdown Structure (WBS) to define project scope. In simple terms, a WBS decomposes the project work into a series of levels, where work definition becomes more specific for each descending level, and specific project items are described at the lowest level. The following is an example:
- A construction project WBS may have a category called Electrical Installations (Level 1).
- That category can be subdivided into sections such as Lighting Installations or Electrical Receptacles (Level 2).
- Specific lighting fixtures are specified in the lighting installations section, as well as their required quantities (Level 3). For example, an item in the list can be described as: Recessed Commercial LED Fixture, 2ft x 4ft, 4000 lumens, clear white light (4100K). This is an item that can be priced specifically by the contractors participating in the bid.
A list of items that is broken down by categories and subcategories is much easier to understand than a plain list where elements from different building systems are combined. An engineering consulting firm can help you put together a WBS effectively. With this bidding format, detecting discrepancies also becomes easier; for example, if five contractors are participating and one of them priced an item significantly lower than the other four, it is likely that there was a mistake or misinterpretation.
Importance of a Technical Point of View
When comparing bids for a project, the opinion of a neutral and qualified third party is highly recommended, and the best recommendation is to hire the services of an engineering consulting or supervision firm. This way, each item on the project scope can be assessed based from the financial and technical standpoint, ensuring that the price provided by a contractor is reasonable according to technical specifications. To define what can be considered cheap or expensive in engineering, a degree of industry know-how is required.
An engineering consultant or firm can also determine if any items in the project scope are priced too high or too low, and then request a clarification from the respective contractor. Low prices are only good news if they are reasonable; unrealistic prices are likely the result of a mistake by the bidding contractor. However, these conclusions can only be reached with a thorough understanding of different building systems and the prices that can be expected.
Equipment Submittals
In simple terms, submittals can be defined as any information on equipment and materials, provided by a contractor for approval before the project is awarded. Some of the most common types of submittals include technical cut sheets, shop drawings and material samples.
Building system components must generally meet a series of requirements and standards. Equipment from reliable manufacturers comes with technical cut sheets, which provide a detailed description of product features and compliance. However, not all contractors work with the same providers, and the contractor selection process may involve comparing equipment from different suppliers for a single item in the project bid. Although equipment cut sheets are available in the Internet, searching for them can be very tedious when dealing with a large project. For this reason, it is very important the contractors participating in a bid provide cut sheets of all the proposed equipment.
Some elements of building systems that perform critical functions or involve a high degree of complexity cannot be described effectively with only textual specifications and general construction plans. In these cases, requesting shop drawings from contractors is recommended, providing specific details on how the component will be manufactured or installed. Shop drawings are especially important in projects that involve custom-built components.
In some projects, it may also make sense to request material samples from the participating contractors, generally with the test results from a qualified laboratory. This is common with concrete, for example, due to how important it is for the structural integrity of a building.
Project Plan: Defining the Timeframe
Contractor bids must clearly define what will provided and at what price, but it is also necessary for them to determine timeframes. This provides a baseline against with the project owner can assess progress, and it is also useful for scheduling intermediate project payments. Completing a project successfully generally involves a detailed planning in terms of time, resources and cost.
- Time: Many project activities follow a logical sequence. For example, roofing installation can only proceed if the underlying structure is already built, and painters must wait for the walls to be completed. A Gantt chart is the best tool for showing the sequence of project activities and their completion times, and it also allows the identification of critical activities that delay the whole project if delayed individually – noncritical activities have a slack time, and can be delayed to a degree without compromising project completion.
- Resources: Engineering projects involve personnel and equipment, and in a well-planned project the contractor knows from the start the activities in which these resources will participate at a given time.
- Cost: After a contractor has developed a Gantt chart and priced each activity, it is possible to estimate a cost calendar. This provides the client a clear idea on how the project budget will be used over time, allowing payments to be scheduled more effectively.
The Project Management Institute places high emphasis on project planning, since it provides a basis against which project progress can be compared in terms of scope, time and cost. When comparing bids from different contractors, verify that timeframes and resource allocation are realistic. A bid can meet all project requirements at a reasonable time, while still being lacking in terms of planning.
Conclusion
When carrying out an engineering project, avoid awarding the job blindly to the contractor with the lowest price. Keep in mind that building systems must meet a series of standards, and there is a limit to how low a specific system can be priced. Also make sure that all bidding contractors provide a detailed project plan, providing details on their expected project timeframes and resource allocation.
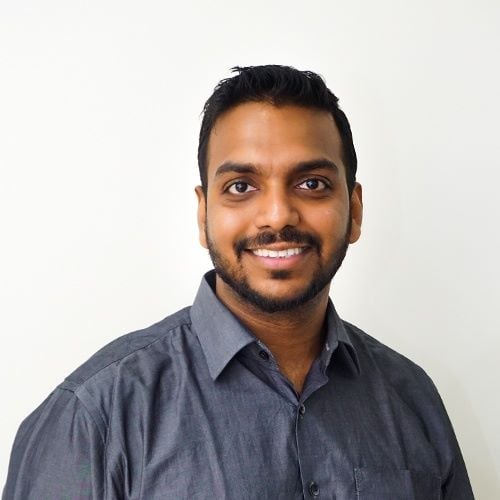
Anuj Srivastava
Anuj Srivastava is a principal partner at NY Engineers. He is known for his MEP franchise market knowledge. Anuj is currently leading a team of 100+ MEP/FP engineers and has successfully led over 1500 franchise projects in the US.
Join 15,000+ Fellow Architects and Contractors
Get expert engineering tips straight to your inbox. Subscribe to the NY Engineers Blog below.