Maximizing Efficiency in Construction Projects Through Value Engineering
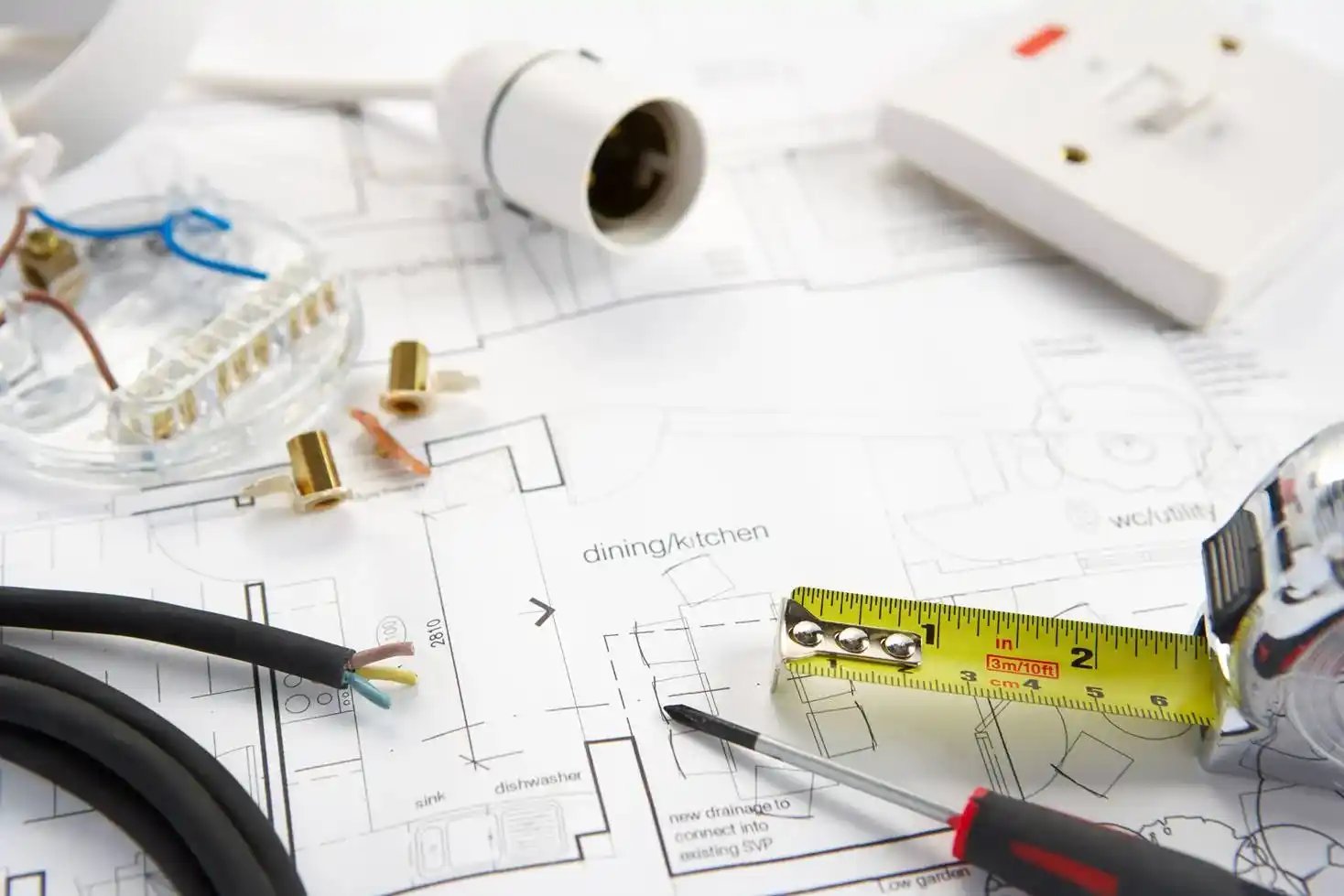
A project must follow a timeline as much as possible. Why is this so? Delays in project completion can significantly impact costs because there’s a need to cover labor costs and other incidentals. With the national average of construction costs up by 5.28 percent year over year, ensuring cost-effectiveness is a priority for all stakeholders.
However, engineers also have to deal with quality maintenance and resource management.
Herein lies the need for value engineering (VE). It's a systematic method that transforms the approach to construction projects. With the concept, everyone, from clients to construction teams, can exercise cost-cutting while elevating the project's value with its inherent quality.
Value Engineering: Its Essence and Principles
While value engineering has many benefits for the construction industry, it was initially intended for manufacturing during the Second World War. The concept operates on the premise that achieving the best possible value involves an in-depth analysis of functionality.
Value engineering lies in its structured thought process. It focuses on maximizing project value through the optimal balance of cost and function.
The concept adheres to principles designed to enhance the decision-making process. These include:
Function-based methodology
This method allows the identification of alternative solutions to meet necessary functions affordably or with a higher value proposition.
For instance, architects can do VE to reevaluate the function of a building component, such as an HVAC system. VE might reveal that a different technology could provide the same comfort and air quality. This principle fosters innovation. It opens the door to exploring non-traditional methods and materials that construction managers might otherwise overlook.
Whole-life cost analysis
This principle refers to the holistic analysis of the construction project. The goal is to have cost-saving measures that don't inadvertently lead to increased expenses down the line.
Multidisciplinary teamwork
The success of value engineering depends on the collaboration of a multidisciplinary team. Diversity makes the team discover different perspectives and expertise. When adequately incorporated, it fosters an environment ripe for innovation because each team member's input is valued and considered in decision-making.
Through teamwork, innovation is possible. For example, an architect can further refine the vision for a building's design by discussing structural materials and techniques with engineers. In this case, they can achieve the desired aesthetic without compromising safety or cost.
How To Apply Value Engineering
Here’s how to do value engineering throughout the project’s lifecycle:
Pre-construction
Even before the start of the project, VE teams should be aligned with the project requirements, including budget and timeline. This stage sets the premise for value optimization.
For example, carrying out a needs analysis will give them a thorough understanding of what the client needs and expects. With this information, they can match it with the budget and see if there are discrepancies. Since they have the data, it will be easier to adjust and align the cost or materials.
Timeline scrutiny is equally important. This process involves setting realistic timelines based on a detailed project analysis. They can do progress reports to track deadlines.
Design phase
During the design phase, VE becomes a collaborative effort, often materializing through sessions with stakeholders. The aim is to scrutinize materials and construction methods.
VE in the design phase includes bringing all stakeholders to explore different design options. They would also discuss implications on cost, quality, and sustainability. The process also includes construction method assessment to find less costly or faster alternatives without compromising the structural integrity.
Construction phase
Plans and designs undergo execution during the actual construction phase. VE analysis should identify potential savings and improvements during this stage. It should cover:
Cost monitoring: This is where teams review costs as the project progresses to identify potential overspending areas and promptly implement corrective measures.
Flexibility and adaptation: Engineers and workers must be agile to adjust to unexpected challenges while focusing on value optimization. At this point, usual challenges include material shortages or design modifications.
Post-construction
Value engineering doesn't stop at project completion. Evaluating the project's performance offers invaluable insights for future VE efforts. It's the perfect time to assess whether the entire construction team achieved the goals set at the start of the project. At this point, teams also get a comprehensive look at how the processes contributed to the project's overall success.
Construction Finance Management Value Engineering
Beyond value engineering principles, construction teams should also take into account the efficiency of their financial operations. Better cash flow management plays a huge role here, and technology integration in financial management becomes invaluable.
Construction companies should analyze how digital financial tools enhance their financial efficiency. This includes setting up online banking services.
For example, they can apply for a checking account online. Some banks have apps that allow users to categorize their spending. Just like their project VE, digital banking can also provide cost savings. They no longer have to drive to the bank to settle their suppliers or deposit payroll for their laborers.
Adopt Value Engineering
Despite the current challenges, value engineering brings operational efficiency across the board. Teams can effectively apply the concept and beat the complexities plaguing the construction industry. At the same, they can deliver projects without sacrificing quality or functionality.
Leverage the transformative potential of value engineering to build a more efficient, sustainable future.
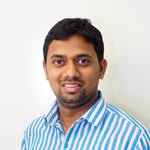
Ravindra Ambegaonkar
Ravindra, the Marketing Manager at NY Engineers, holds an MBA from Staffordshire University and has helped us grow as a leading MEP engineering firm in the USA
Join 15,000+ Fellow Architects and Contractors
Get expert engineering tips straight to your inbox. Subscribe to the NY Engineers Blog below.