Plaza Decks: Overview and Design Features
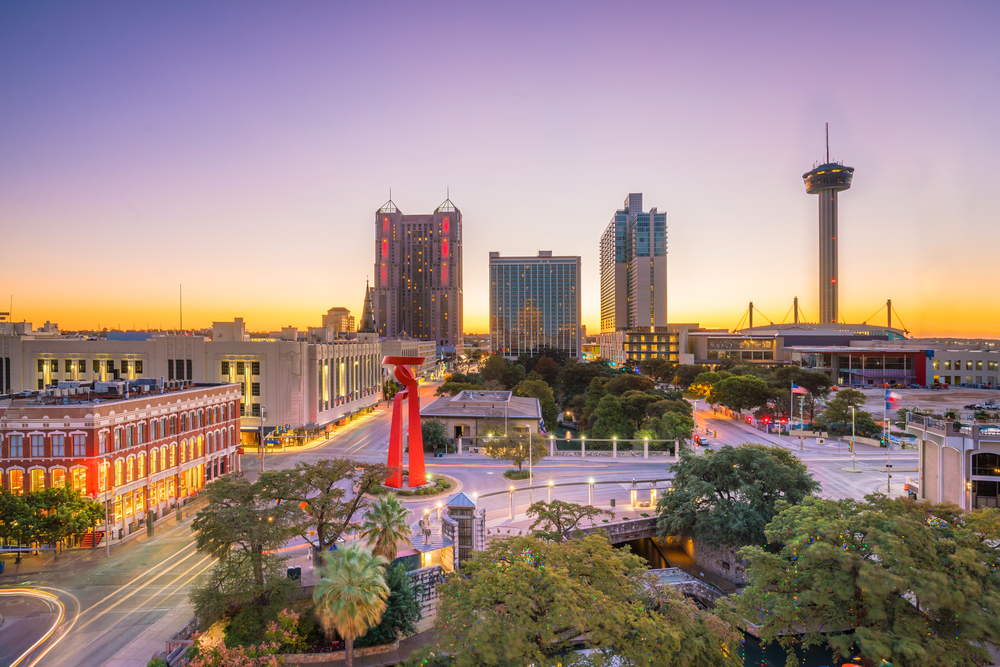
A plaza deck is any supported slab that provides a greenscape or areas for vehicle and pedestrian movement over occupied space. Plaza decks should not be confused with roof assemblies, which are only exposed to the weather and in some cases light foot traffic. Due to the higher loads they experience, plaza decks have additional design requirements beyond the basic waterproofing characteristics.
Plaza decks are more complex and maintenance-intensive than roofs, but usually they are not designed with the same level of detail. The vehicular use of plaza decks will depend on the type of structure, and is usually limited to cleaning equipment and light vehicles. However, under special circumstances, plaza decks may be required to support heavy equipment like trucks or construction equipment.
Optimize your building envelope: improve insulation and control humidity.
As with other structural systems exposed to the weather, the design and application of waterproofing for plaza decks is crucial. The design should also consider protection, drainage and thermal considerations. Plaza decks are subject to some of the highest levels of wear and deterioration among structural systems: they are exposed to harsh moisture conditions, thermal effects and traffic. In some cases, the design conditions for plaza decks are comparable to those of parking lot slabs.
Plaza decks can fail due to poor construction, inadequate design or unexpected loads. Other common issues include severe moisture, chemical effects and poor selection of construction materials. The main design considerations for plaza decks are described below: structural support, environmental control, finishing, and interfaces with other building systems.
Structural Support Considerations for Plaza Decks
Plaza decks consist of structural slabs and beam elements that are subject to high loads - dead and live. Dead loads come from the deck itself, soil, planters, pavers, fountains, structures, mechanical systems, etc. On the other hand, the main live loads acting on plaza decks are pedestrian traffic and vehicular traffic. Some buildings have special requirements for pedestrian areas, such as emergency vehicle loads.
Structural support systems for plaza deck areas are usually made from cast-in-place concrete systems, either reinforced or post-tensioned. Precast concrete elements are not recommended for plaza decks, due to the difficulties in creating effective joints and surface waterproofing.
Environmental Control
Plaza decks are subject to environmental factors like thermal effects, soil ingress, tree roots, moisture and noise. Thermal effects and humidity can also come from internal sources. The performance and service life of plaza decks will depend on their ability to withstand and control these environmental effects - internal and external.
Among the environmental effects that act on plaza decks, moisture is the most critical. Typically, a moisture control screen or barrier is designed to control water ingress into the structure.
- The first line of defense against moisture is an upper screen layer at the exposed surface. This serves as protection against rain, snow, and even irrigation systems.
- This upper screen can consist of permeable landscape areas, and impermeable pavers like concrete and asphalt.
- The effectiveness of the upper surface will influence the design requirements of other moisture control elements.
Moisture that crosses the upper screen of a plaza deck must be directed towards the exit drains. This is normally achieved by using a drainage system that consists of granular materials. Contrary to other structural systems that require only vapor retarders, plaza deck designs must include a waterproofing membrane, to control water effectively at horizontal surfaces.
Thermal considerations may be a concern in shallow plaza decks. In these cases, insulation may be provided on the top or below the structural ceiling element. Insulation also plays a key role in moisture control, preventing condensation on the interior surfaces of a plaza deck.
Finishing Systems for Plaza Decks
Plaza deck systems have both internal and external finishing considerations.
- The interior finish is dependent on the usage of indoor spaces. For example, finishes for controlled office environments are different from those used in parking environments.
- Typical finishing options for plaza decks include paint, stucco and framed walls with drywall. In some cases, the finished surface of a construction material like concrete is enough.
MEP Distribution Systems in Plaza Decks
MEP distribution systems in plaza decks are commonly located within the structural slab. These systems can be electrical conduit, heating systems, mechanical piping, plumbing, etc. Plaza deck soil areas may also contain mechanical installations and sprinkler lines.
Consider that some MEP installations may have indoor and outdoor components. Waterproofing and weather resistance are important design considerations for external components, and also when MEP components are installed through a slab.
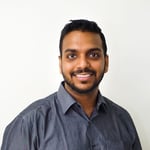
Anuj Srivastava
Anuj Srivastava is a principal partner at NY Engineers. He is known for his MEP franchise market knowledge. Anuj is currently leading a team of 100+ MEP/FP engineers and has successfully led over 1500 franchise projects in the US.
Join 15,000+ Fellow Architects and Contractors
Get expert engineering tips straight to your inbox. Subscribe to the NY Engineers Blog below.