Prefabrication in MEP Systems
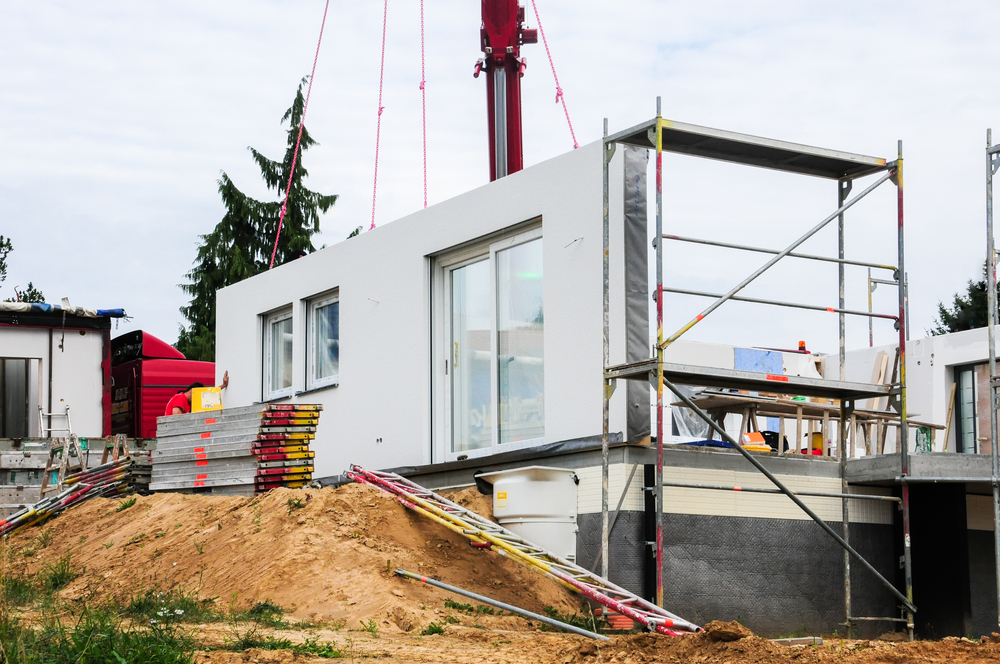
Prefabrication is an impactful innovation in the construction industry, with the potential to greatly reduce waste while speeding up projects. Prefabrication can be applied in many areas of construction projects, and the method has also been implemented successfully for building systems - mechanical, electrical and plumbing (MEP) installations.
What is MEP Prefabrication?
Prefabrication consists of manufacturing and assembling components offsite, and then transporting them to the construction site for installation. These assemblies are known as MEP modules or prefabricated MEP modules. Prefabrication takes part of the MEP installation process to a controlled factory environment, in isolation from external factors like the weather and urban traffic.
Speed up your project and reduce waste with a prefabricated MEP design.
MEP Prefabrication VS Traditional Methods
Traditionally, MEP construction has been a process with multiple steps, where different specialists bring their skills at a certain point during the project. Coordinating multiple teams is a challenge, and some common problems include inefficient use of labor, weather delays, unsafe working conditions, inefficient waste management, high traffic onsite, and maintaining a high quality. All these issues can raise project costs, while causing delays.
MEP prefabrication provides an alternative to traditional methods. MEP components and modules can be designed, manufactured, inspected and tested offsite. Plumbers, HVAC technicians, electricians and other tradesment can work together more easily in a controlled manufacturing environment. Coordination and collaboration between trades is completed faster, speeding up MEP installations.
Types of MEP Prefabrication
Prefabrication can be used to manufacture modules of variable scale and complexity, ranging from simple prefabricated components to fully functional assemblies.
TYPE OF PREFABRICATED MODULE |
EXAMPLES |
1) Prefabricated components |
Flexible sprinkler droppers Flexible pipes Plug and play cables Pre-insulated air conditioning ducts Pre-insulated plastic piping |
2) Prefabricated sub-assemblies or modules |
Vertical riser modules: Consist of vertical riser ducts and pipes. The vertical services in each module can be installed horizontally at ground level in the factory and branch out to several floors. Vertical riser modules can be installed prior to the erection of riser shaft block walls, they can also be lowered into the riser shaft through designated openings. Horizontal ceiling modules: It should contain most, if not all, of MEP services components in the ceilings, such as:
Pump and compressor modules. |
3) Prefabricated Sub-Assemblies with Architectural/Structural Components |
Riser modules with platforms MEP modules attached to catwalks Horizontal modules with ceiling boards |
4) Fully Integrated Assemblies |
Prefabricated MEP plant modules are completely pre-assembled with all the necessary control panels, instruments and interfaces to properly installed them on site, this fully integrated assemblies include:
|
MEP Prefabrication Procedure
Design Phase
During this stage, the main participants involved are MEP engineers and other specialists.
- Design drawing submissions
- Coordinated drawings for factory
- Production drawing submissions
- Material submission
The completed drawings and schedule of materials is approved and finished.
Factory Plant
During this stage, the participants involved are contractors and fabricators.
- Material procurement
- Prefabrication of modules
- Quality check, verified by professional engineers
Modules are stored safely, and then transported to the construction site.
On-Site Assembly
During this stage, the main participants involved are contractors and subcontractors, under the guidance of a supervision staff.
- Visual inspection of delivered modules
- Modules are moved to the installation position
- Marking and setting out module positions
- Modules are installed and connected to mains
- Testing and commissioning for the entire installation
Benefits of Prefabrication
MEP prefabrication has transformed the building construction industry in many ways. This section discusses some of the main benefits.
Faster completion: The module manufacturing and assembly process begins offsite, without waiting for the construction site to be ready. This also enables for mass production for large projects, or groups of projects with similar modules.
Efficient use of skilled labor: Technicians can apply their knowledge better in a manufacturing facility that is free from external disruptions.
Easy installation: Prefabricating and installing MEP modules is easier than completing a building with conventional construction methods.
Less hazardous environment: Prefabrication uses controlled and safe working environments both offsite and onsite. Scaffolding work is minimized and lifting operations are greatly reduced.
Less onsite traffic: Most of the work is completed offsite and transported, which also leads to a safer jobsite.
Less weather delays: Since prefabricated components are made in factories with controlled environments, the impact of weather is minimized.
Cost savings: Prefabrication requires an initial investment to purchase and coordinate the equipment. However, the total amount of work is reduced and completed faster, which leads to cost savings.
Damage prevention: MEP modules are installed from the ground up, avoiding many connection problems. Onsite work is limited to connecting modules with mains, which minimizes the potential damage to components.
Quality control: High quality is guaranteed, since most of the work is completed in a controlled factory environment.
Reduced environmental impact: Dust, noise pollution and construction waste are significantly reduced with off-site prefabrication.
Key Aspects for Successful MEP Prefabrication
Many common issues in MEP prefabrication can be avoided with an adequate design. Accurate drawings increase productivity, while preventing rework. Some key aspects for successful MEP prefabrication are:
- Accurate information
- Precise drawings
- Qualified drafters with experience
- Building Information Modeling knowledge
- Constant collaboration and communication between the involved parties
- Provisions for future maintenance
Building Information Modeling in MEP Modular Construction
Building information modeling (BIM) is ideal for design coordination, construction planning, on-site delivery planning, clash detection, and prefabrication planning in modular construction. BIM facilitates communication between all parties involved in building projects - designers, architects, engineers and contractors can also get involved during the early stages of a project.
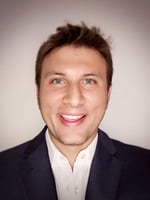
Michael Tobias
Michael Tobias, the Founding Principal of NY Engineers, currently leads a team of 50+ MEP/FP engineers and has led over 1,000 projects in the US
Join 15,000+ Fellow Architects and Contractors
Get expert engineering tips straight to your inbox. Subscribe to the NY Engineers Blog below.