Reasons Why Carbon Fiber is Preferred for Manufacturing Aircraft
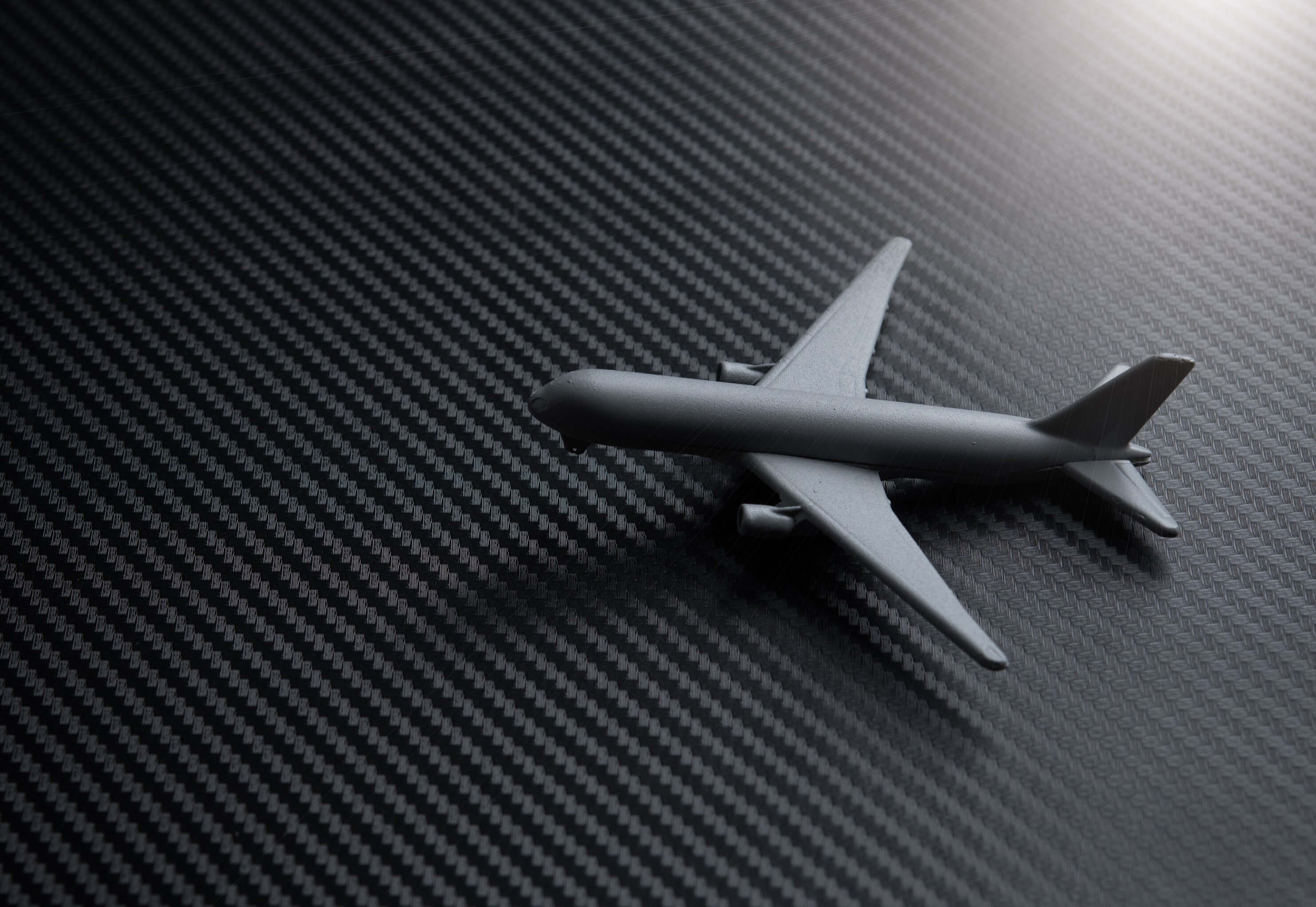
Carbon fiber composite products are gradually becoming the future solution in aviation engineering. The excellent aesthetics we see in the Airbus A350 XWB and the Boeing 787 Dreamliner is just about the tip of the iceberg to what carbon fiber material is capable of. Commercial airlines are buying into the efficiency of aerodynamics design, light, and strong material.
An aerodynamic and light aircraft means fewer parts requirements and a significantly reduced fuel cost for commercial airlines. Over a large scale, these savings margins open up capital and allow airlines to expand their business and increase demand for aircraft manufacturers.
Increases Fuel Efficiency
In the airline industry, it’s no secret that a light aircraft is more fuel-efficient and relatively cheaper to operate. One of the highest costs of operating an aircraft is fuel, and reducing the cost ran by it significantly decreases the overall cost of operating the jets. With a 20% reduction in weight, it is no surprise that aircraft manufacturers and airlines are leaning towards carbon fiber composite material when manufacturing aircraft.
A lighter aircraft doesn’t mean it’s less robust; carbon fiber composite is incredibly strong for its weight. However, although these savings are marginal, they add up, and aviation experts estimate $1 million in savings over a single aircraft’s life span.
Improves Aerodynamic Performance
Many factors are contributing to an aircraft’s fuel efficiency, and one of the significant influencers is aerodynamic performance. This kind of performance comes because of new, sleeker designs. Manufacturers now rely on the flexibility and strength of carbon composite material to design aircraft bodies to optimum aerodynamic performance. When this is achieved, aerodynamic drag can be reduced by up to 5%, cutting fuel consumption on a larger scale.
Reduces the Number of Parts
Carbon fiber manufactured aircraft see a significant cost reduction because they need fewer parts to hold the structure together. Using traditional materials like aluminum, the massive Airbus A380 approximately requires about six million pieces. With the new carbon fiber composite parts, it is possible to combine many parts in one mold, and that greatly reduces the number of components used in the manufacturing process.
The collective cost reduction using carbon fiber composite materials includes less staff in the production line, less time is spent manufacturing, and fewer parts needed means saving manufacturing and maintenance costs.
Future Aircraft Designs
Engineering technology is ever improving in many industries that are seeing the benefits of it. With many benefits enjoyed by the aviation industry offered by current carbon fiber innovations, the future of aircraft only looks promising. Aircraft designers are given more freedom to push past current limitations, guided by aviation regulations when it comes to fuel efficiency and aerodynamics. The future of commercial aircraft designs will aim to increase fuselage space, allowing more passengers and classes while striving to meet the highest safety standards.
We are seeing many of these new innovations and technology, particularly in military aircraft. These new aircraft designs will impact and improve all forces acting on aircraft’s performance, lift-to-weight, and lift-to-drag ratios.
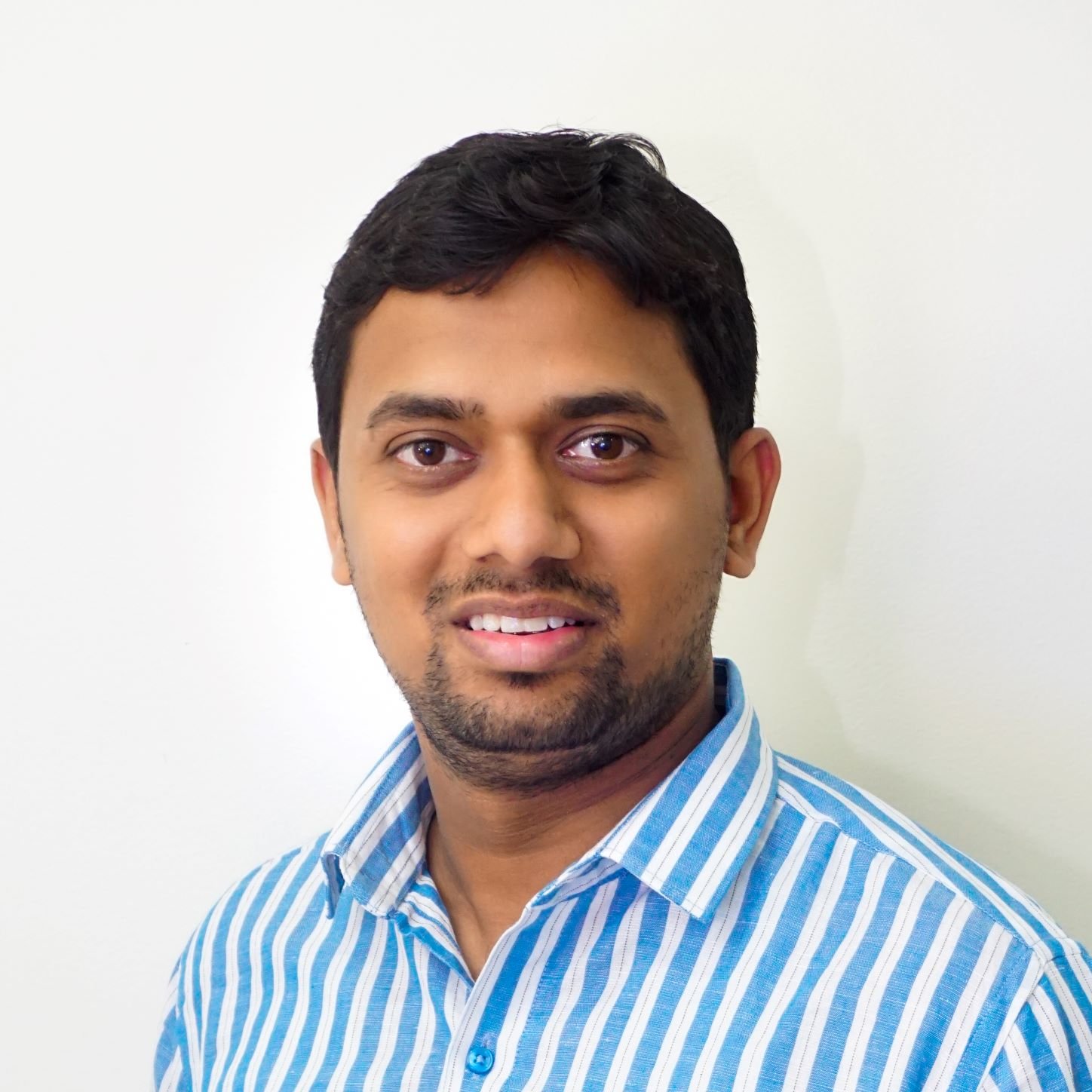
Ravindra Ambegaonkar
Ravindra, the Marketing Manager at NY Engineers, holds an MBA from Staffordshire University and has helped us grow as a leading MEP engineering firm in the USA
Join 15,000+ Fellow Architects and Contractors
Get expert engineering tips straight to your inbox. Subscribe to the NY Engineers Blog below.