Steam Use in Large New York City Buildings
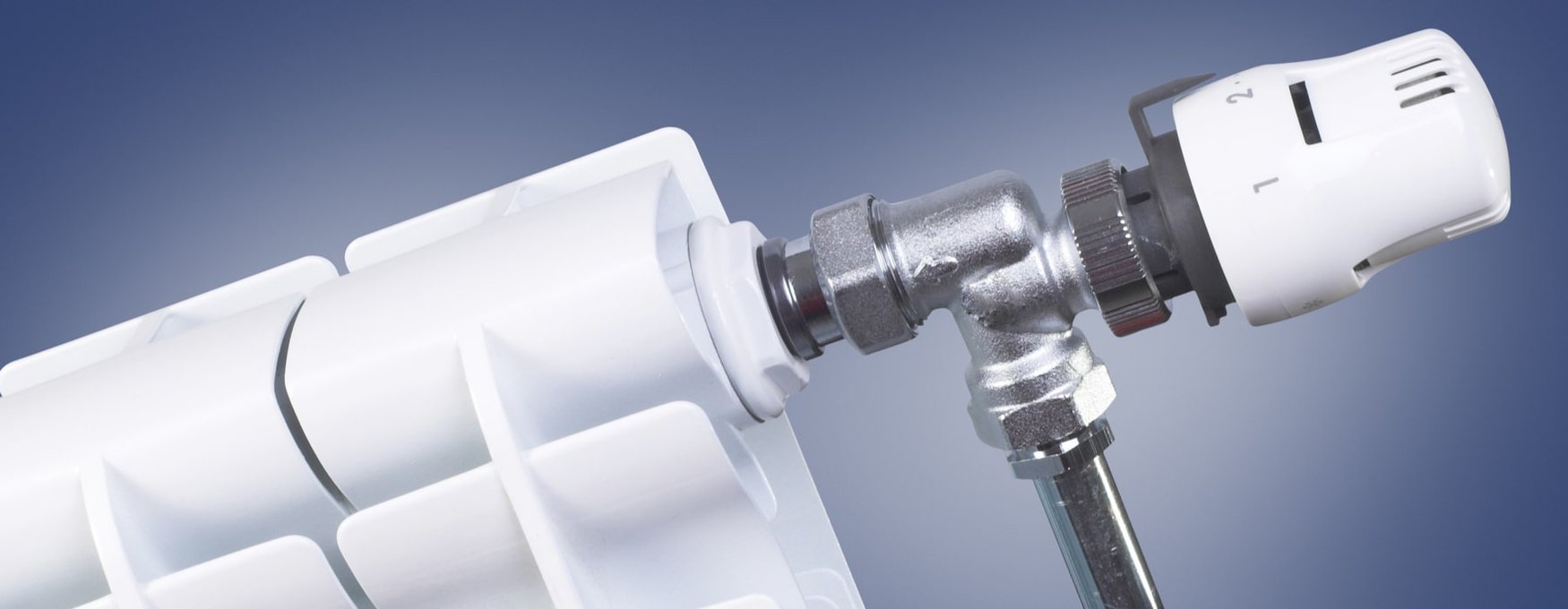
Although hot water is preferred for heating systems in new constructions, steam is still widely used in older NYC buildings. Data collected through the Greener, Greater Buildings Plan (GGBP) reveals that most buildings above 50,000 square feet still use steam-based space heating.
- 72.9% of buildings have steam boilers fired by natural gas or fuel oil, while 10% rely on Con Edison’s district steam service. In other words, 81.9% of heating systems in large NYC buildings still use steam.
- Hot water boilers are in second place, accounting for 13.4% of heating systems, while all other configurations represent less than 5% of heating systems.
With respect to heat distribution, 68.1% of heating systems use steam pipes, while 26% use hydronic piping. Direct electric heating and forced air distribution are found in less than 6% of NYC buildings above 50,000 square feet.
Natural gas is the most common heat source for steam boilers, followed by heating oil, and the majority of these steam boilers are found in multifamily residential buildings. The Urban Green Council has determined that upgrading these steam systems to more modern configurations is one of the most promising areas of opportunity to improve energy efficiency in NYC, while reducing greenhouse gas emissions.
Steam based systems offer the advantage of not requiring a pump, since steam rises to individual radiators by itself, and that is the main reason why old buildings have them. However, for a given heating load, a steam-based system will consume much more fuel than a hot water system using a boiler and pumps, producing more emissions as a consequence. In order to meet its emissions reduction goal of 80% by 2050, New York City will have to phase out steam heating in its buildings - it is one of the most carbon-intensive heating system configurations.
Main Limitations of Steam-Based Heating Systems
The two main limitations of steam-based heating systems are inefficiency and a slow response time. In the first place, the process of boiling and condensing water is less efficient that simply heating and distributing water without a phase change. In addition, the slow response of steam-based systems limits the use of automatic controls, which are very effective for saving energy and improving comfort when deployed in more modern heating systems. When a steam boiler is adjusted, there can be a long wait time before there is a noticeable change in the heating output of radiators.
Steam-based heating systems also suffer from a design limitation that may cause discomfort for occupants. Some of them are very old, when NYC building codes required heating loads to be calculated assuming open windows, causing indoor spaces to be overheated. Keep in mind that airtight building envelopes are a modern design trend from the late 20th century, while many NYC buildings are from before World War II.
Other than being inefficient, steam-based heating systems can also be demanding in terms of maintenance, and this applies for both one-pipe and two-pipe configurations.
- The air vents in one-pipe radiators are prone to failure. When they become clogged, steam cannot flow freely into the radiator, reducing the heating output. On the other hand, an air vent stuck in the open position results in a constant steam leak into living space, which raises indoor humidity and may also cause a severe burn if touched.
- In the case of two-pipe systems, steam traps can also be locked in either the open or closed position. This causes a system imbalance, where some areas may be poorly heated while others are overheated.
One-pipe steam systems are more common in low-rise residential constructions, accounting for 37% of all audited area in the multifamily sector according to the Greener, Greater Buildings Plan. On the other hand, two-pipe steam systems are more common in high-rise residential constructions, accounting for 25% of the audited area. One-pipe steam heating systems are the most inefficient configuration, using around 13% more energy than the median value for all audited buildings.
Poor energy efficiency, a slow response time and demanding maintenance increase the ownership cost of a steam-based heating system. The main reason why these systems are still so common is that an upgrade can be very expensive: walls and floors must be demolished to remove steam lines, and rebuilt after the installation of hydronic piping. The piping diameters required are also very different for a steam and hot water distribution, and in the case of one-pipe steam systems there is no return line to send water back to the boiler. In addition, many radiator models are not suitable for conversion to hot water.
Upgrading Steam-Based Heating Systems
If a major renovation is planned for an older building with steam-based heating, an upgrade to hot water distribution is highly recommended. Since many building areas are changed completely during a major renovation, the heating system upgrade is less disruptive. Water-source heat pumps, one of the most efficient heating options currently available, require hydronic piping to operate.
Many buildings use their steam boilers for domestic hot water systems as well. In the summer, when space heating loads are reduced, steam boilers operate well below their rated load with a drastic drop in efficiency. However, since these domestic hot water system already have piping, their conversion to a more modern and efficient technology is much easier than for space heating systems.
Conclusion
Steam was a convenient heating medium one century ago, thanks to the advantage of not requiring a water pump. However, the price to pay is using much more fuel that a hot water boiler, and also using it less efficiently. Although a heating system conversion can be an expensive building upgrade project, it becomes much simpler if programmed along with a major building renovation. Steam heating is also a very carbon-intensive process, which does not align with the emissions reduction targets established by New York City. Even if the new hot water boiler uses natural gas, it will generally be of smaller capacity and more efficient.
Property owners considering an upgrade for their steam-based heating systems can get in touch with a qualified engineering firm to get an assessment of their buildings. If the steam-based heating system is considered suitable for conversion, the upgrade cost is significantly lower.
Make sure your mechanical installations are code compliant and energy efficient, while getting a 50% faster turnaround. You can contact Nearby EngineersNew York Engineers by email (info@ny-engineers.com) or phone (786) 788-0295212-575-5300.
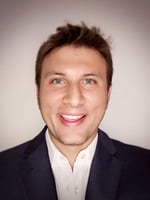
Michael Tobias
Michael Tobias, the Founding Principal of NY Engineers, currently leads a team of 50+ MEP/FP engineers and has led over 1,000 projects in the US
Join 15,000+ Fellow Architects and Contractors
Get expert engineering tips straight to your inbox. Subscribe to the NY Engineers Blog below.