The Complete Architect Design Checklist for MEP Engineering Projects
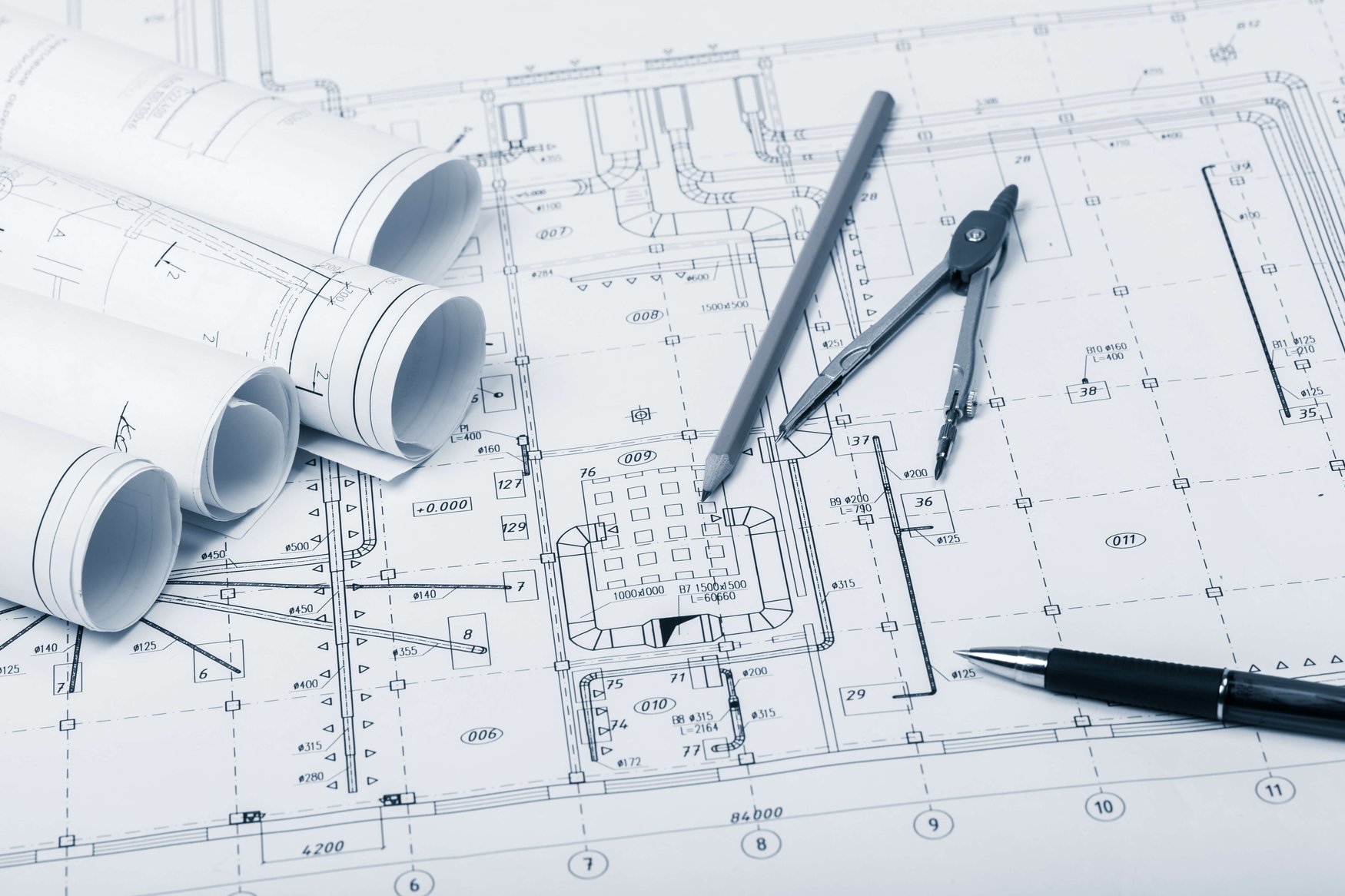
Today, MEP engineering projects are a major trend driving a process of change within the building industry, and for good reason. MEP integrations establish the link between the architect’s design and the engineering systems.The practice facilitates the design changes and influences the building’s structural and architectural concepts. Choosing an MEP engineering project allows teams to recognize potential problems in the early design stages, reducing unexpected setbacks during construction. When done properly, an architect can use the information provided in the initial MEP analysis to design the perfect layout for the building that will make the entire construction process run smoothly.
However, when it comes to designing MEP integrations, many architects overlook essential steps that result in inefficiencies down the line. Because MEP integrations are heavily reliant on good design, it's crucial that architects know what they need to do to ensure successful delivery early on. Using these tips as a checklist for your next MEP engineering project will help you minimize risk for error, and be confident every detail is accounted for.
Avoid costly delays on your next project. Get your MEP design reviewed before you start construction to ensure successful delivery.
Overview of MEP Engineering Projects 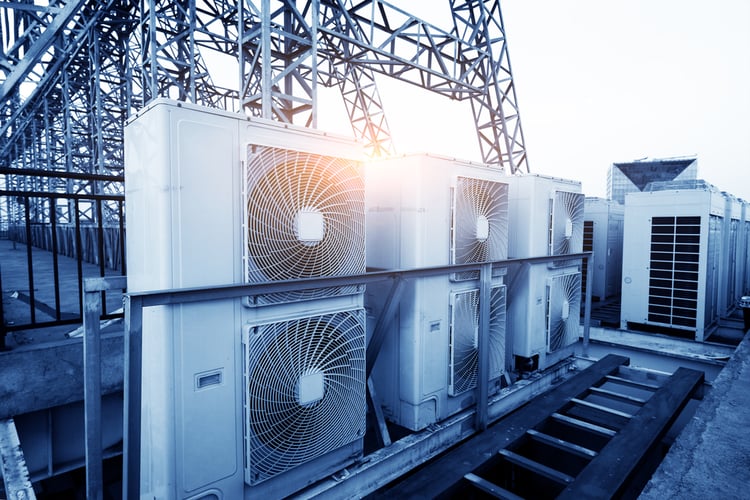
The first step of a MEP engineering project involves gauging the scope of services. Historically, the mechanical, electrical, and plumbing systems fall under MEP categories. Today, technology plays a much larger role in the process - it’s ingrained in every aspect of building. MEP integrations now include fire protection systems, controls, process piping and data communication lines. The MEP engineering and architectural design reviews identify potential problems prior to construction. The added value of MEP for the client is a functional and cost efficient structure.
The process starts by checking the architectural design model. Using the architect's conception, engineers ensure the architect's building design fits the construction requirements. This step allows teams to identify the potential flaws or obstacles early on, which greatly benefits the build schedule. Without this step, these conditions could delay trade schedules due to the necessary revisions and time limitations. By performing this analysis beforehand, the design team can ensure the delivered project is code compliant.
Common Challenges with Designing MEP Integrations
Thanks to advanced technologies available for MEP integrations, the proper sized equipment is able to be identified in the early design phase. The engineering dimensions and space requirements are critical during the early stages of design. Although it seems like a small step, the cost savings generated from this information helps keep the project on budget. In some cases, the architect may lose some design space to accommodate the equipment. In this situation, they would be faced with the challenge of adjusting the design layout without affecting the building’s engineering systems. The process allows the suggested MEP integrations to be installed the building’s construction plans. These alterations must be accomplished without loss to function or safety.
Even small issues can turn into big problems. Issues like equipment being placed in the wrong location can have consequences to the building’s structural design. One example is equipment placed on the roof. Due to the size and location, these systems may require structural re-enforcement. Generally, cooling equipment placed on roof tops have moving parts, which can cause noise and vibrations, requiring revisions to the building’s structure to accommodate the weight and noise. Structural revisions at any phase of the project can be a pain. Early detection can reduce the cost of revisions and the amount of valuable work hours.
Like all industries, construction has a norm for quality and completeness of work. Construction problems are usually related to structural load capacities, system controls and safety regulations, but he most expensive mistakes are errors tied to the project’s larger applications. When rework is required, it's typically because the original designs and construction reviews missed the error. Ongoing communications throughout the project's construction between engineering and the architect avoid costly modifications.
Early Owner Involvement
The preliminary work needs to involve the building owner. Getting the owner involved early on is important so architects can be sure their design meets the clients standards and avoiding numerous revisions. For this reason, owner input is valuable to designing and planning a cost-effective project. Specifically with MEP integrations, the information generated from the initial MEP analysis provides a realistic cost of the project and the potential changes. Based on the MEP data, the building owner can make final decisions the project's design and build in the early stages, rather than later on in the process when changes are more difficult and costly. By resolving these issues early on, the value of the design increases.
Address any Pre-Existing Conditions
All cities and states have code enforcement requiring pre-construction evaluations of existing buildings. The evaluation includes structural, and MEP systems. MEP integrations help determine the potential constraints of the building. However, not all pre-existing conditions are obvious. A building corridors, sheer walls, fire walls, and ceiling types have a tendency to hide the past. Conditions could include termite damage, dry rot and removal of mold and asbestos.
Coordinate with Other Team Members
In MEP integration, the importance of clear communication with team members with differing roles in the project lifecycle is often underestimated. Coordinating MEP engineers, synchronizing contractors, and updating project management is key to keeping the project on track. The interaction of mind sets and approaches keeps everything running smoothly. MEP integrations include heating, ventilation and air conditioning (HVAC), plumbing and electrical systems. Prior to the final drawings, the MEP project engineer prepares a detailed preliminary. The final design reviews, technical specifications and cost estimates are based on the analysis. The team ensures the final design is compliant and includes verifications of approved equipment. The engineering checklist preserves the building’s planned systems without changing the architect’s illustration.
Consider the Cost-Benefit Ratio of MEP Design
To design for maximize value, MEP engineering designs should generate a cost ratio greater than 1. Basically, the formula is why architects and MEP engineers are building structures faster. Today’s technology has introduced a method of adding modifications to retrofit existing buildings. Using current technology, engineers are improving the building’s internal systems. The modified results include longer lifecycles of equipment. The design process is not limited to just the architecture. Urban planners, city authorities and engineers impact the final build. The architect and MEP engineering teams ensure it’s built to last. They are responsible for delivering the project on-time and within budget. At the same time – the client expectations are met and the future occupants are comfortable and safe.
Key Takeaways
Creating a design for MEP engineering projects is a complex process, and there are a lot of elements that must be considered in order to create a design that launches the project for success early on. Some issues are technical, while others relate to industry standards, processes and practices. Follow these tips on your next project to increase your chances of successful outcomes.
-
From time to time, the teams have to realign and find the best way to implement change to the structure’s design.
-
Forcing an engineering process into an existing condition is not always a practicable solution.
-
MEP is tailoring technology to a specific set of building designs and construction conditions.
Want to be confident your MEP Design is built for success? Request a free MEP value engineering design review and we'll perform a detailed analysis of your design, locate any areas for improvement, and get your costs down to their minimum requirement.
Nearby EngineersNew York Engineers has a MEP design track record of 1,000+ projects. Contact us via email (info@ny-engineers.com) or phone (786) 788-0295212-575-5300, and make sure your building systems meet codes.
Editors Note: This post was originally published in November 2016 and has been revamped and updated for accuracy and comprehensiveness.
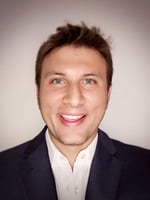
Michael Tobias
Michael Tobias, the Founding Principal of NY Engineers, currently leads a team of 50+ MEP/FP engineers and has led over 1,000 projects in the US
Join 15,000+ Fellow Architects and Contractors
Get expert engineering tips straight to your inbox. Subscribe to the NY Engineers Blog below.