MEP Engineering Tips: 7 Ways to Minimize Mechanical Space
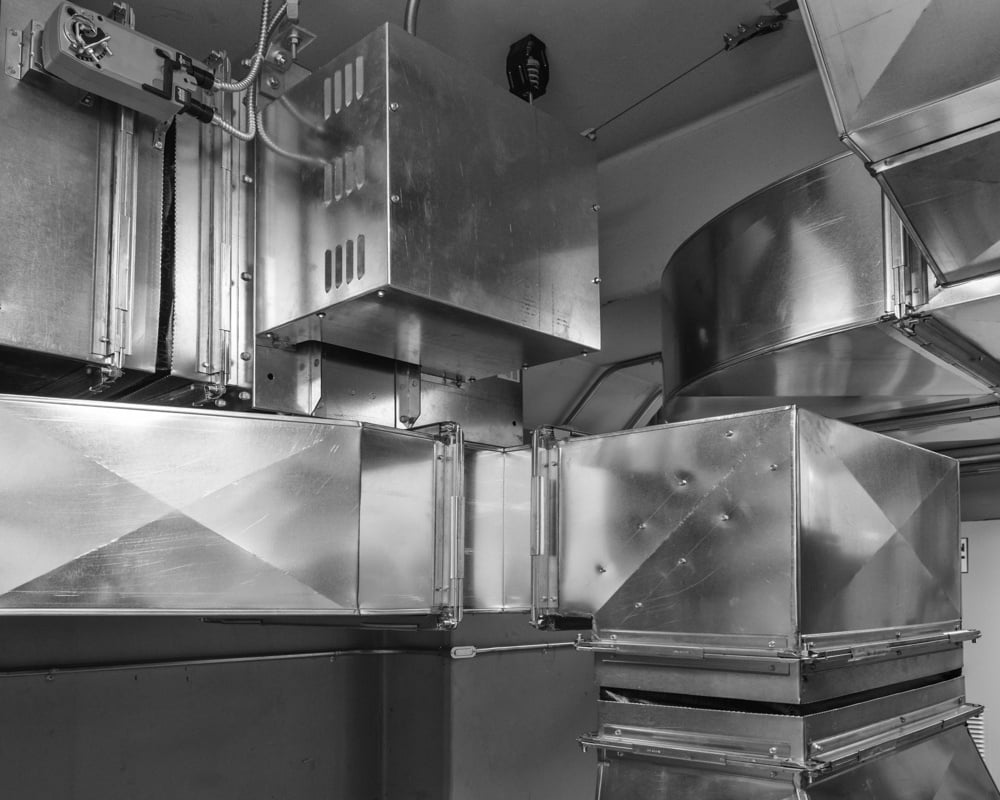
In any MEP engineering project, the Mechanical equipment carries out a fundamental role in residential, commercial, and industrial locations, performing functions such as:
- Space cooling and heating
- Supplying chilled or hot water
- Refrigeration
- Ventilation
- Indoor humidity control
These types of equipment and their associated ductwork and piping are notorious for their high space requirements, but there are several ways to make mechanical installations more compact.
1) Installing Boilers as Close to the Roof as Possible
Boilers that operate with the combustion of fuels such as oil, propane, natural gas, biomass, or biodiesel require a chimney to exhaust their flue gases. Since the chimney must cross the entire distance from the boiler to the rooftop, its space requirements are increased as the boiler is located farther from the uppermost level – there are more floors to go through.
Installing a boiler at the highest possible location in a building shortens the chimney, which offers three significant advantages:
- The space that the chimney would have used on each floor is freed up for other purposes.
- The installation becomes safer, because the risk of flue gases being released indoors is minimized.
- The cost of the chimney is reduced.
An alternative to installing boilers on the attic or the uppermost floor of a building is to simply use a heating technology that does not require a chimney, such as an electric resistance heater or a heat pump. A solar water heater is also a viable option: it is located on the rooftop, saving indoor space, and it runs with sunlight, a free energy input.
Over-engineering drives up costs without any benefit. Learn what systems prevent over-engineering so you can avoid unnecessary expenses.
2) Installing Air Conditioning Units on Ceilings
The largest individual component of an air conditioning system is typically the condenser, which is normally located outdoors. When installed on the external walls of a home or building, condensers occupy plenty of space and may even represent an obstacle for outdoor circulation if located on the first floor.
Condensers also release a lot of heat, and the circulation of warm air may be restricted when outdoor spaces are reduced due to proximity with another building or a wall. This has two negative consequences: warm air can make outdoor locations uncomfortable, and it reduces the operating efficiency of condensers. On the other hand, if a condenser is located on a rooftop, warm air can circulate more freely, and noise becomes less of an issue.
In large commercial or industrial facilities, the equipment used by air conditioning and cooling systems is much larger, but the same logic applies – installing these units on rooftops saves considerable outdoor space. However, this is only feasible if the structure is strong enough to support the weight. Examples of equipment that may be found outdoors in a typical commercial or industrial MEP engineering project settings include:
- Packaged rooftop air conditioning units
- Air-cooled chillers
- Cooling towers for industrial processes or for water-cooled chiller plants
3) Using the Same System for Cooling and Heating
A heat pump operates with the refrigeration cycle, the same physical principle on which air conditioners are based, with the difference that it operates in reverse – it extracts heat from the cooler outdoor environment and uses it for space or water heating. In addition, some heat pumps are reversible, which allows them to consolidate heating and cooling into a single piece of equipment.
Upgrading to a heat pump can also result in energy efficiency improvements. There are two key pieces of information to look for when comparing heat pump models:
- The Seasonal Energy Efficiency Ratio (SEER) is the ratio of cooling output to energy input during the cooling season.
- The Heating Seasonal Performance Factor (HSPF) is basically the same concept, but for when the heat pump is operating in heating mode.
The SEER and HSPF are ratios that relate BTUs (British Thermal Units) and watt-hours, and a higher value translates into reduced energy consumption: it means the unit needs less energy to meet a specific cooling or heating load. For example, an air conditioner with a SEER of 20 will only draw half the power of a SEER 10 unit, assuming both have the same cooling output.
Alternatively, unit efficiency may be reported as a Coefficient of Performance, which is also a ratio of cooling or heating output and power input, but using watts for all quantities. Heat pumps typically have a COP of 2.5 or more, which means they yield significant savings when replacing resistance heaters, whose COP is 1.
In MEP engineering, an ideal scenario for upgrading to a heat pump would be if a household uses a resistance heater and an old air conditioning unit. In this case, a heat pump would consolidate two devices into one, while improving energy efficiency in both modes of operation.
For industrial applications, using an absorption chiller is a viable option for consolidating heating and cooling systems. This type of chiller can use waste heat from a steam plant or an industrial process, and provide cold water for space and process cooling. It is important to note, however, that absorption chillers are viable only when there is sufficient waste heat; otherwise, a normal compression-based chiller is a better choice.
4) Installing Mechanical Equipment in Normally Unused Spaces
Another viable strategy to minimize the useful indoor space on your next MEP engineering project that is typically taken up by mechanical equipment is to install these units in a location that is not normally used. One example of such locations is:
- Roof Bulkheads – This is one type of structure that is found on many buildings and is rarely used. Their main purpose is providing access to the roof, and they tend to be used more during construction and maintenance than during actual building operation.
5) Using Mini-Split Systems Instead of Packaged Rooftop Units for Small Buildings
Packaged rooftop units allow multiple condensers to be consolidated as a single unit, but they require considerable space for ductwork. In small residential and commercial locations, mini-split systems are often the superior choice, offering a simpler installation and superior energy efficiency. Packaged rooftop units normally go up to SEER 15, while mini-split systems are available with efficiency ratings of SEER 25 or above.
Mini-split systems are a practical choice in commercial locations that are split into several zones with independent schedules, such as open-air shopping malls. As locations become larger, rooftop packaged units emerge as the preferred choice – too many compressors and evaporators would be required to offer air conditioning with mini-split units.
6) Vertically Aligning Equipment on Several Floors
Multi-story buildings normally have components that are repeated floor by floor, and mechanical equipment is no exception to this. For example, air conditioning systems in tall buildings often use a central chiller plant to cool water, which is then supplied to air handling units (AHU) that cool the air in each floor.
If AHUs and similar units are aligned vertically floor by floor, it is possible to distribute cold water to all of them with a single pipe running vertically across the building. Since ductwork is installed above the false ceiling, most mechanical equipment will be located out of sight.
The associated electrical installations providing power to mechanical equipment also become more compact when similar units are aligned vertically or horizontally. Multiple circuits can be installed within a single conduit run, and it is also possible to use a bus duct for equipment drawing high current.
7) Hiring Qualified Professionals for the Design Stage
A well-organized mechanical installation takes up less space, and making sure the layout is as simple as possible is a process that starts from the project design phase. If mechanical, electrical, and plumbing installations (MEP) are designed together, equipment and associated components can be specified and located with the following goals in mind:
- Minimizing the space and materials requirements.
- Avoiding clutter caused by components from different buildings systems.
There are now software packages that allow 3D MEP models to be created and visualized before starting the construction process -- including Revit, which we use at New York Engineers. These models are of great assistance when planning how mechanical installations will be laid out on your next MEP engineering project, and are also very useful for contractors during materials takeoff and construction.
Conclusions
Optimizing the space used by mechanical equipment in your MEP engineering projects offers several advantages beyond comfort. It may be possible to reduce the cost of installations, and in many cases it also increases energy efficiency. The best way to ensure a mechanical installation offers top performance and an optimal layout is to hire qualified designers and contractors for the project.
Have any tips for minimizing mechanical space? Comment below to share your space saving tips and download our free ebook, "The Top 5 Most Over-Engineered Building Components" to learn what systems prevent over-engineering so you can avoid unnecessary expenses.
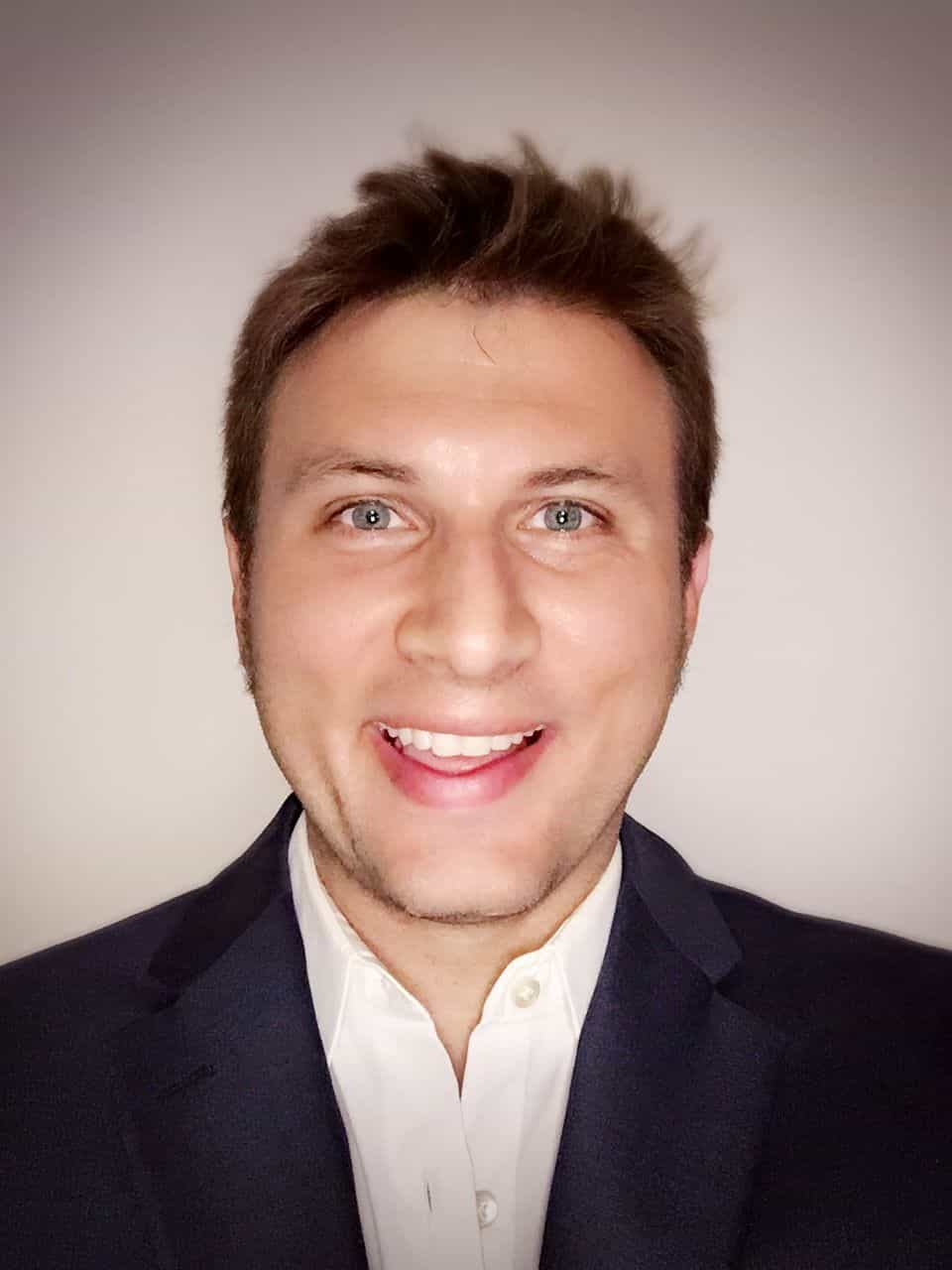
Michael Tobias
Michael Tobias, the Founding Principal of NY Engineers, currently leads a team of 50+ MEP/FP engineers and has led over 1,000 projects in the US
Join 15,000+ Fellow Architects and Contractors
Get expert engineering tips straight to your inbox. Subscribe to the NY Engineers Blog below.