Welding Hazards and How to Avoid Them
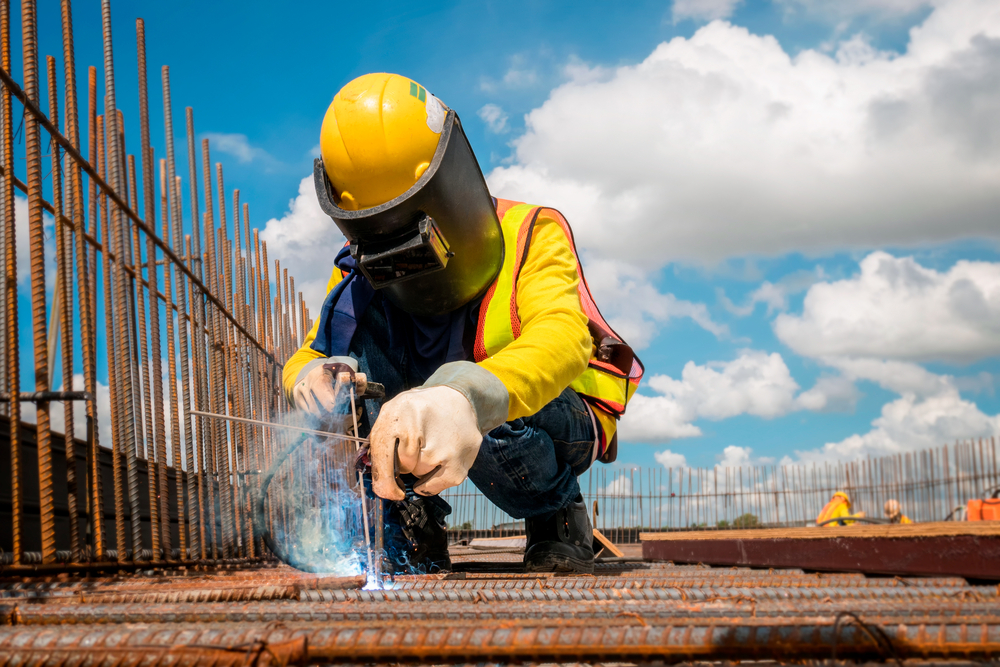
Welding is a procedure in which two metals are heated, melted and mixed to produce a joint between them. Welding is a technical field of its own, covering over 70 different welding procedures. Some common types are Shielded Metal Arc Welding (SMAW), Gas Tungsten Arc Welding (GTAW) and Submerged Arc Welding (SAW).
Welding procedures have certain health hazards for operators and surrounding workers, which include exposure to metal fumes and ultraviolet radiation. Welding, cutting and brazing operations also come with the risk of accidents like burns, eye damage, electric shock and cuts. Most of these hazards can be prevented with engineering controls, training and personal protective equipment (PPE). Preventing accidents during welding is an important element of construction site safety.
Our construction management services make the building process safer and more efficient.
Most Common Welding Hazards
As mentioned before, welding creates hazards for both welders and those working in the vicinity. It is important to be aware of the risks associated with welding, and the precautions to prevent accidents and injuries. Here is a list of the most common hazards and risks welding poses:
Electric Shock
During arc welding procedures, live electrical circuits are used to melt metals. This creates a risk of electric shock, which happens when a welder touches two metal objects that have a voltage difference between them. Electrocution is a serious hazard when welding, and it can result in severe injuries or death. Even if the electric shock is not lethal, it can cause welders to lose balance and fall from a high surface (Source: Welderhub.com).
Electric shock incidents are classified into two categories: primary voltage shock and secondary voltage shock.
- Primary voltage shock is extremely dangerous, since it ranges from 230 to 260 volts. It can occur by having direct contact with the inside of welding equipment and other grounded metals.
- The most common type is secondary voltage shock, which occurs when touching part of the electrode circuit, ranging from 20 to 100 volts.
A higher voltage can produce a higher current, and there is an increased risk of dying from electrocution. A shock of 50 volts can be enough to injure or kill an operator, depending on the conditions.
The key to avoiding electric shock is proper insulation, and all equipment should be dry and in good condition. The following recommendations can reduce the risk of electrocution while welding:
- Avoid touching the metallic parts of the electrode holder, especially if your skin or clothing are damp.
- Welders should wear dry gloves in good condition.
- Provide rubber mats or other types of insulation for welders.
- Perform lockout and tagout procedures when doing repairs, only qualified technicians should repair welding equipment.
- Perform proper inspection of welding equipment and electrode holder before working.
- Take extra safety measures when working on humid places, metal structures and cramped conditions where it is necessary to kneel or work on uncomfortable positions.
Fire Hazards
Welding generates sparks that spray up to 35 feet and may cause fire hazards. When this happens, workers with grease on their clothing have the highest risk of getting burned. Flammable chemicals should always be kept away from welding spaces, to avoid any fire that may damage the entire facility. The following measures can help prevent fire during welding:
- Keep a fire extinguisher on hand.
- Declutter the working space.
- Store combustible substances like gasoline, wood, cardboard and flammable chemicals away from the working space.
- Use fire-resistant shields if flammable materials can’t be moved.
- Dusty locations can generate additional risks when welding. The high concentration of fine particles can oxidize without warning, which may result in a flash fire or explosion.
Fumes and Gases
Welding exposes personnel to invisible gaseous fumes like ozone, nitrogen, chromium oxides, nickel oxides and carbon monoxide. The level of damage depends on the gas, concentration and exposure duration. Some illnesses caused by welding fumes and gases are pneumonia, asthma, cancer and metal fume fever. The effects can also include irritation of the throat, lungs, and eyes. The following recommendations can minimize exposure to fumes and gases:
- Keeping the head out of the fume plume.
- Use ventilation and local exhaust to remove harmful gases.
- Use approved respiratory devices when ventilation is insufficient.
- Monitor contaminant levels to determine air quality.
- Read the material safety data sheet (MSDS) for the electrodes to know which fumes will be released.
Physical Hazards
There are many physical hazards present during welding activities, such as burns, eye damage, cuts, and crushed fingers. Physical hazards can be drastically reduced with adequate Personal Protective Equipment (PPE). Appropriate PPE for welders includes:
- Welding helmets with side-shields: Helmets provide protection against UV radiation, particles, debris and chemical burns. Adjusting lens filters is necessary to protect the eyes but also to see clearly while working.
- Respirators: Provide protection against gases and fumes.
- Fire resistant clothing: Reduces risks of burns caused by heat, fire and radiation.
- Ear protection: Offers protection against workplace noise hazards and vibration.
- Boots and gloves: Insulated flame-resistant gloves and rubber-soled hard toe boots protect welders from hazards like electric shock and falling objects.
Conclusion
Welding safety measures are designed to protect workers from hazards present during welding procedures. To minimize health issues and safety injuries at worksites, training sessions and the regular inspection of welding equipment are important. Workers should be made aware of the hazards present during welding activities, and the corresponding precautions.
Nearby EngineersNew York Engineers has a MEP design track record of 1,000+ projects. Contact us via email (info@ny-engineers.com) or phone (786) 788-0295212-575-5300, and make sure your building systems meet codes.
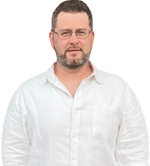
Keith Fink
Keith is the Franchise Brand Manager at NY Engineers, Keith is all things related to our project portfolio, brands and all things you need to know before we start your project.
Join 15,000+ Fellow Architects and Contractors
Get expert engineering tips straight to your inbox. Subscribe to the NY Engineers Blog below.