Contech: Promising Solutions for the Construction Industry
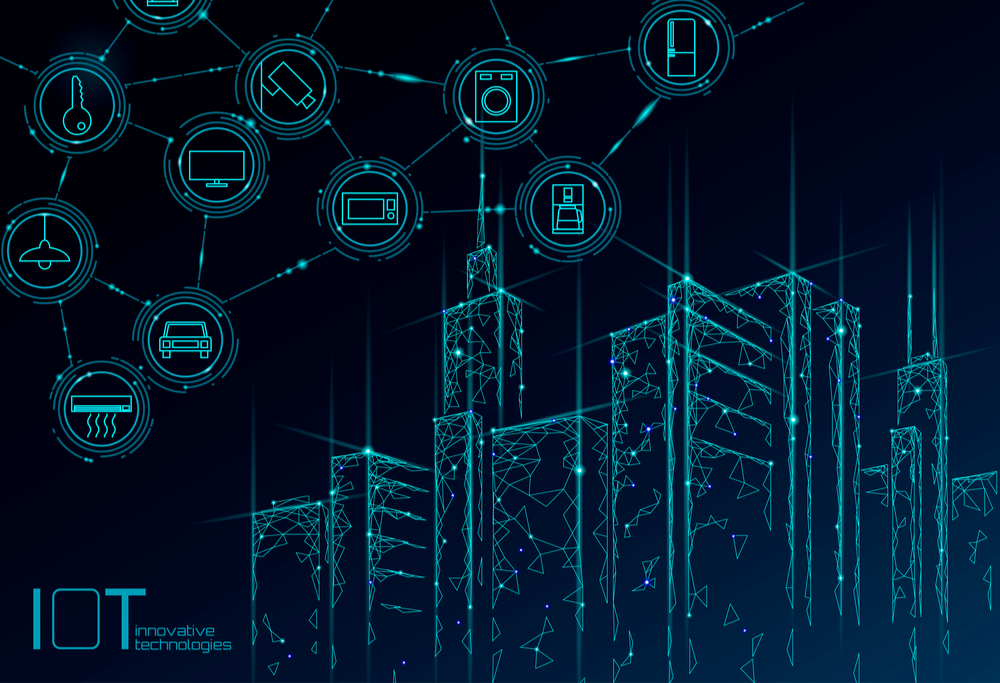
Modern information technologies and advanced software are changing all business fields, and the construction sector is no exception. Just like the term “fintech” is used in the financial sector, “contech” is used to describe technology for the construction industry. Contech can make the building process more efficient, less wasteful, and safer for everyone involved.
- According to Construction Dive, annual investment in tech firms increased from $352 million in 2016, to $6 billion in 2018.
- Ernst & Young predicts that some contech solutions will become industries worth over $100 billion annually by 2025.
The construction sector is being disrupted by the coronavirus outbreak in 2020. However, contech offers solutions to keep critical projects moving during the emergency, and to reactivate suspended projects after the outbreak. Like any business transformation, contech will take time to be adopted in the construction industry. However, technologies that contribute to social distancing will have high demand during the COVID-19 outbreak and its aftermath.
Design and manage your building project more efficiently with the latest engineering technology.
This article will provide an overview of some key technologies with promising applications in the construction industry.
Virtual Reality and Augmented Reality
Virtual reality (VR) and augmented reality (AR) are sometimes confused, but there are important differences between them. VR refers to 100% virtual environments that can be “visited” with headgear, creating a simulation of reality. On the other hand, AR blends reality and VR: data and virtual components are overlaid in the field of vision when visiting a construction site or existing building.
In the construction industry, the main value of VR and AR is providing information more effectively. Instead of meeting to discuss plans and specifications, owners and construction professionals can view a virtual model of the project. When visiting the site, they can view how pending work fits in with completed work. Tradesmen and maintenance personnel can also use AR to visualize mechanical, electrical, and plumbing installations more clearly.
Wearable Technology
Construction work can be risky, even when strict safety guidelines are implemented. However, wearable technology can help reduce accidents, while ensuring a quick response if they happen. Project site personnel can be provided with wearable devices that detect environmental hazards while sending automatic alerts if an accident occurs.
Fall detection is a promising application of wearable tech. Construction workers can wear a sensor that detects sudden changes in vertical position. This sensor will not activate when walking down a staircase, since the movement is slow, but it will detect a fall because the movement is fast.
With the coronavirus outbreak, getting infected is added to the list of project risks. Wearable tech can also be used to enforce social distancing in critical projects that must continue during the outbreak. If everyone on the site wears sensors that detect proximity, social distancing is easier to track. The device can also give automatic notifications to users when they are working too close to each other.
BIM and Digital Twins
Building Information Modeling (BIM) is the evolution of conventional 2D plans and specifications. The building and its components are modeled in 3D, adding detailed information such as physical properties and cost. BIM can also include time-based information such as delivery and installation schedules, operational data like energy consumption, and maintenance data like component wear.
BIM is associated with 3D building models, but that is only a small part of BIM. There are now complex models that use up to 7 dimensions, according to EY:
- Three spatial dimensions - length, width, and height (3D)
- Scheduling and construction times (4D)
- Cost estimation and tracking (5D)
- Sustainability information (6D)
- Operations and maintenance information (7D)
With modern design and simulation software, creating a digital twin of a building is possible. A digital twin is much more complex than a 3D model - it is an identical replica of the building in a virtual environment, which is constantly updated with live data. The digital twin includes technical and financial information while allowing simulations and predictions.
Digital twins can be used to optimize a building design and manage the construction process more efficiently. Once the building is completed, a digital twin can be used by the maintenance department to track the condition of equipment and components. When planning building renovations or equipment upgrades, a digital twin can be used to simulate many options before spending capital on one of them.
Data Collection: Drones, Laser Scanning and Sensor Networks
Contech brings promising innovations to the building sector, but many of them require large amounts of information. For this reason, data-gathering solutions are an important part of contech - some examples are drones, laser scanning, and sensor networks.
Laser scanning is very useful when gathering information about an existing facility. This is not an issue in new constructions, since information is created by architects and engineers during the design phase. However, when modeling an existing building, engineers must first gather all types of information - dimensions, material properties, component specifications, etc.
- This process can take weeks in a large facility, but laser scanning makes it much faster.
- Instead of measuring the dimensions of all building components manually, engineers can simply set up the scanner to sweep the facility by areas.
- The geometric model of the facility is produced semi-automatically, and engineers can concentrate on adding specifications and properties that cannot be scanned.
Drones have promising applications in areas like topography, project supervision, and safety management. They can even carry small tools and materials to construction sites. Drones can observe construction work from viewpoints that are inaccessible to humans, and supervisors fly a drone instead of walking in dangerous areas.
During health emergencies like the COVID-19 outbreak, drones can also be used for social distancing. Personal interaction in project sites is reduced when drones are used for observation and supervision.
Sensor networks can be used in existing buildings to gather real-time data about equipment and components. For example, if building operation and maintenance are managed with a digital twin, a sensor network can keep the twin updated. Sensors can also detect issues in building areas that are hard to reach for visual inspections.
Construction Robots
When the concept of construction automation is mentioned, we may think about robot workers. However, a smarter approach is adding artificial intelligence and automatic controls to existing tools and equipment.
Automation can perform simple tasks that produce repetitive strain injury (RSI) in construction workers. It can also be used for tasks that involve hazards like high temperature or voltage, such as arc welding. Rather than replacing human workers, automation can be used to enhance their productivity while improving safety.
3D Printing
According to Ernst & Young, 3D printing will have the highest growth among contech solutions in the coming years. By 2025, 3D printing is expected to grow by over 240% percent, becoming a $500 million industry.
The value of 3D printing comes from creating building elements and system components locally, instead of relying on material supply chains and scheduled deliveries. This is especially useful if urgent work must be completed, and an important component is missing - it can simply be 3D printed instead of relying on suppliers.
The use of 3D printing may be limited if a component uses rare materials or a complex manufacturing process. However, when this is not the case, 3D printing is a fast and effective solution to produce components locally.
Conclusion
Contech can make the construction process much more efficient while creating safer working conditions. There are many emerging technologies in the building sector, and some could become multibillion-dollar industries in less than a decade. Architects, engineers, and contractors who adopt these technologies early will gain a major competitive advantage.
In the short term, contech solutions can help construction firms through the coronavirus outbreak. Technologies that enhance collaboration while reducing personal interaction can be used to keep urgent projects moving, and to reactivate suspended projects when possible.
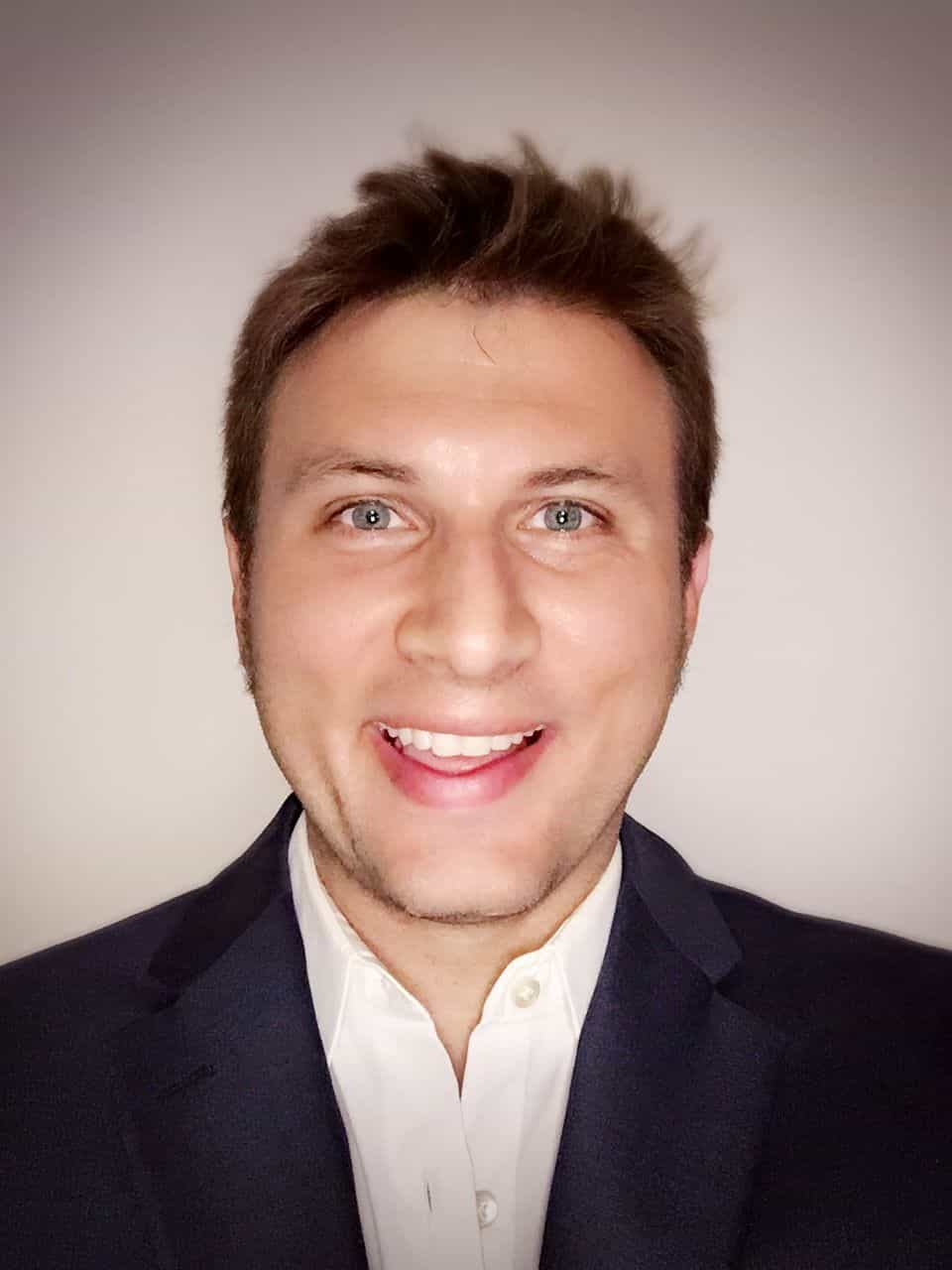
Michael Tobias
Michael Tobias, the Founding Principal of NY Engineers, currently leads a team of 50+ MEP/FP engineers and has led over 1,000 projects in the US
Join 15,000+ Fellow Architects and Contractors
Get expert engineering tips straight to your inbox. Subscribe to the NY Engineers Blog below.