How a Project Plan Simplifies the Construction Process
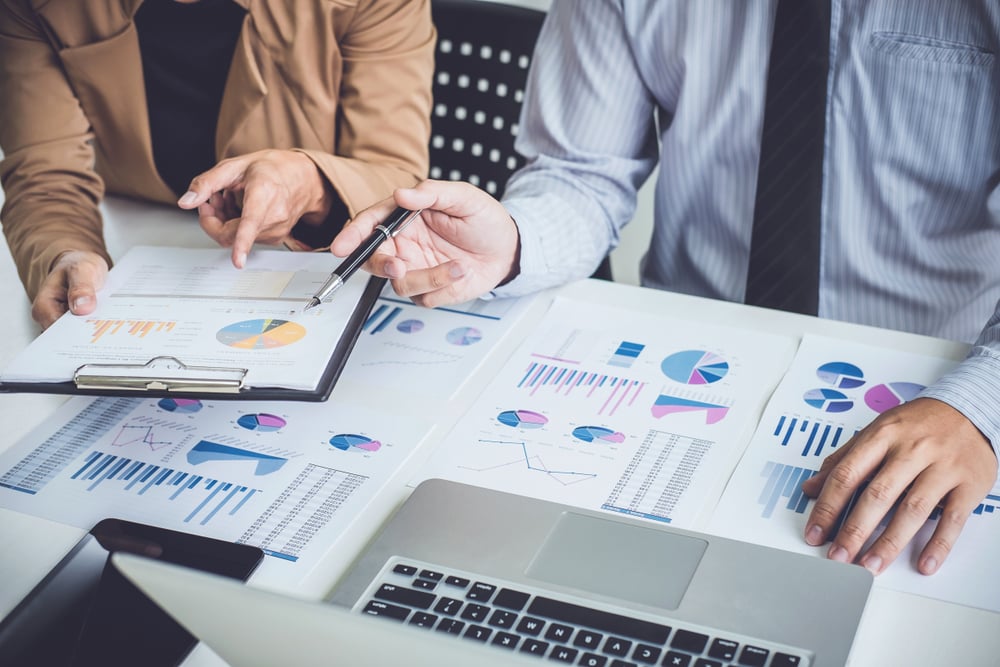
Since every project is different, construction management brings unique challenges. Unlike assembly line manufacturing, where the goal is to produce a large number of identical products, the construction process delivers a customized building according to the needs of each client. Also consider that most construction activity is performed outdoors, where weather conditions can cause delays.
Building projects also require effective coordination between many suppliers and contractors in the short term. There is no time to establish a complex supply chain, like those found in conventional manufacturing.
Working with qualified engineers and architects during the design phase contributes greatly to project success. However, you must also ensure that the construction process follows the requirements in design documents, while meeting a budget and a deadline. A project plan is a very effective tool to meet these requirements.
Simplify building construction with effective project management.
Using a Project Plan Effectively
Project management is a very broad topic, and it would be possible to write entire books about it. However, to adopt the best practices in project management successfully, you need a project plan. There are many software solutions that allow the creation of project plans, and there is no specific format. However, a project plan will normally provide the following information:
- A Work Breakdown Structure (WBS), which is a detailed breakdown of the project scope.
- The sequence of activities, normally represented in a Gantt chart. Activities follow a logical sequence - for instance, electricians cannot install wiring before conduit.
- A project schedule, which is based on the Gantt chart.
- Project cost and resource schedules, which are based on the expenses and inputs allocated to each activity.
A project plan is very useful because it provides a baseline to compare the progress of construction. The actual project is compared with the plan at regular intervals, considering time and cost along with the scope of work completed. Based on how these three metrics interact, project managers can draw conclusions.
For example, if the accumulated expenses by a certain date exceed the planned expenses, it is not possible to reach conclusions right away. Consider the following possibilities:
- If the project is ahead of schedule and expenses are consistent with the work completed, the outlook is positive. The accumulated expenses are higher simply because the project is moving faster.
- On the other hand, if the project is on schedule or delayed, extra expenses indicate waste. The extra funds being spent are not converted into progress in this case.
A project cannot be monitored based only on one metric, since this can lead to incorrect conclusions. The percentage of work completed does not provide direct information on how the budget is being used, just like expenses are not a direct indicator of work completion.
When a project is compared with the baseline at regular intervals, issues can be identified and fixed before they have a major impact. For example, cost overruns and delays can be identified when their magnitude is still small.
Managing Project Resources Effectively
The construction process of a building uses many resources. In addition to construction materials, a project needs tools, equipment and skilled labor. There is also a significant energy input, since many types of equipment consume fuel or electricity.
A key advantage of the project plan is that is provides a clear picture of when each resource is required. For example, if a building is still in the excavation and foundation phase, there is no need to have electricians and HVAC technicians on site. Likewise, if a project uses sensitive materials near the end of the construction process, there is no point in delivering them to the site at the start of the project.
However, waiting until the last possible moment to order materials or equipment is not the best approach either. Consider that many product have a lead time, and they cannot be delivered to the construction site on demand. For example, if a piece of HVAC equipment is installed on the 6th month of a project and its delivery takes one month, the order must already be placed by the 5th month.
The project plan is also useful for managing and tracking the presence of subcontractors on the project site. For example, if the Gantt chart indicates simultaneous activities that involve HVAC and plumbing, technical staff from both areas will be present at that time.
The availability of resources also influences planning decisions. For instance, if two activities require the full attention from a specific contractor, they cannot be scheduled simultaneously.
Conclusion
To deliver a building successfully, project managers must balance the work progress, budget and time. With a reliable project plan, the work completed can be inspected regularly to detect and fix issues.
Buildings represent a business decision for developers, and investors seek to maximize the return on their capital. Cost overruns are detrimental, since the benefits per dollar spent are reduced. In the case of buildings that are being developed for rent, a delay means that the owner must wait longer before receiving rent payments.
When effective project management is combined with professional design services, developers can expect an improved outcome in construction projects. Solid project management keeps the construction process on time and on budget, and a good design reduces ownership costs.
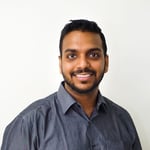
Anuj Srivastava
Anuj Srivastava is a principal partner at NY Engineers. He is known for his MEP franchise market knowledge. Anuj is currently leading a team of 100+ MEP/FP engineers and has successfully led over 1500 franchise projects in the US.
Join 15,000+ Fellow Architects and Contractors
Get expert engineering tips straight to your inbox. Subscribe to the NY Engineers Blog below.