How Modular Construction Can Help Prevent Disruption in Projects
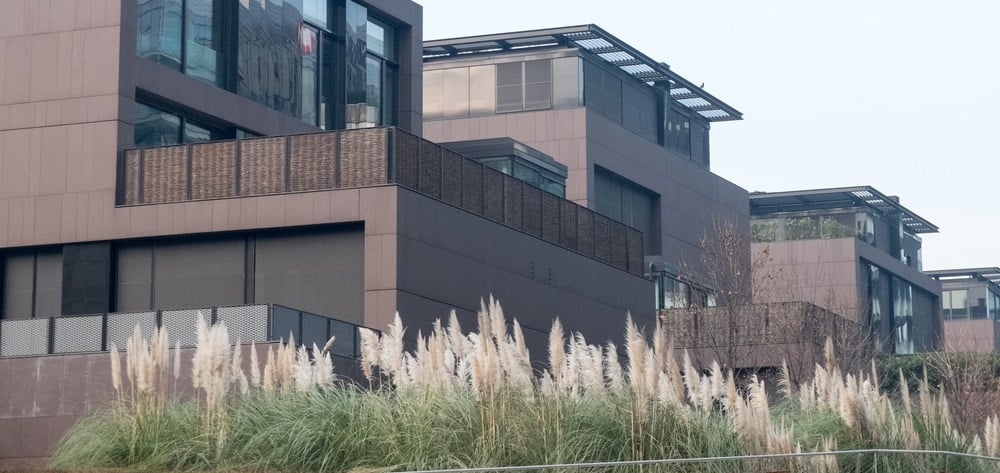
Construction is the largest industry in the world, representing 14% of global GDP according to the business consulting firm McKinsey & Company. However, building projects can be disrupted by several external factors, and risk management becomes critical to protect investments. External threats for construction projects include extreme weather, volatile material costs due to geopolitical issues, and health emergencies like the COVID-19 pandemic.
Modular construction is promising, since it brings many advantages of the manufacturing industry to building projects. Most of the construction process is taken to a factory floor, isolated from external factors like traffic and the weather.
A controlled factory environment also increases quality while reducing waste. Personnel can also be monitored more easily in a factory, which improves safety. This includes the implementation of coronavirus prevention measures such as social distancing.
How Modular Construction Reduces Project Delays
When modular construction is used, most man-hours of work happen in a manufacturing facility. As a result, the amount of materials and equipment at the project site is greatly reduced. Most of the site work consists of assembling the prefabricated modules. These procedures can be scheduled for days with favorable conditions, while prefabrication continues regardless of the weather.
On the other hand, when traditional construction methods are used, many activities must be suspended when the weather is unfavorable. If two building projects have similar scope, but one uses modular construction while the other doesn’t, the first one is less likely to experience delays.
Consider that modular construction also isolates the project from day-to-day disruptions, such as heavy traffic around the project site. Procedures that involve heavy materials and equipment are also isolated from the public, which helps prevent accidents.
Improving Work Safety with Modular Construction
Another advantage of modular construction is taking workers to a factory floor, where managers have more control compared with a building site. For example, work at height is greatly reduced, since modules can be manufactured at ground level. Assembling the modules at the project site may still involve some work at height, but the time and staff involved are reduced.
During an emergency like the coronavirus pandemic, a factory environment also simplifies the use of prevention measures. This has been a major challenge for construction managers on project sites.
- Some construction methods make social distancing impossible, especially when they involve teamwork in reduced spaces.
- PPE such as face coverings can be very uncomfortable for construction workers, particularly when the weather is hot. PPE can also interfere with the gear worn in some skilled trades, such as welding helmets.
- Due to the layout of construction sites, monitoring all the personnel can be impractical. As a consequence, situations that increase the risk of COVID-19 infection may go undetected.
These issues are reduced or mitigated in a manufacturing plant. Social distancing can be enabled with an adequate working layout, indoor conditions can be controlled to reduce the discomfort caused by PPE, and the staff can be monitored more easily. Modular construction is also better suited for the use of robots, in cases where social distancing is not possible. Robots can also be used for tasks like welding, where the PPE that is normally required interferes with the PPE for coronavirus prevention.
Want to ensure 50% faster project completion time with cost-effective modular designs?
Adapting Financing for Modular Construction
Modular construction offers many advantages, but one of the main barriers is finding adequate financing for building projects. If you compare how cash flow is distributed throughout a project, there are important differences between traditional construction and modular construction:
- In traditional construction, expenses are spread more evenly throughout the building process. For example, if a project will take several months, materials are normally purchased in batches. Purchasing all the materials upfront requires plenty of cash, and storing them for a long time is risky and impractical.
- In modular construction, activities that would normally follow a sequence can be completed simultaneously. For example, modules from different floors can be fabricated at once. As a result, modular construction consumes a larger fraction of the project budget upfront.
Banks and other financial institutions normally provide the funds for construction as the project is completed, instead of releasing the full loan upfront. However, this must be adapted for modular construction, where upfront expenses are higher than in traditional projects. With access to more financing options, modular construction would be possible in a larger number of projects.
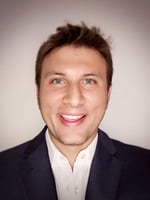
Michael Tobias
Michael Tobias, the Founding Principal of NY Engineers, currently leads a team of 50+ MEP/FP engineers and has led over 1,000 projects in the US
Related Posts
Join 15,000+ Fellow Architects and Contractors
Get expert engineering tips straight to your inbox. Subscribe to the NY Engineers Blog below.