Building Information Modeling for Modular Construction
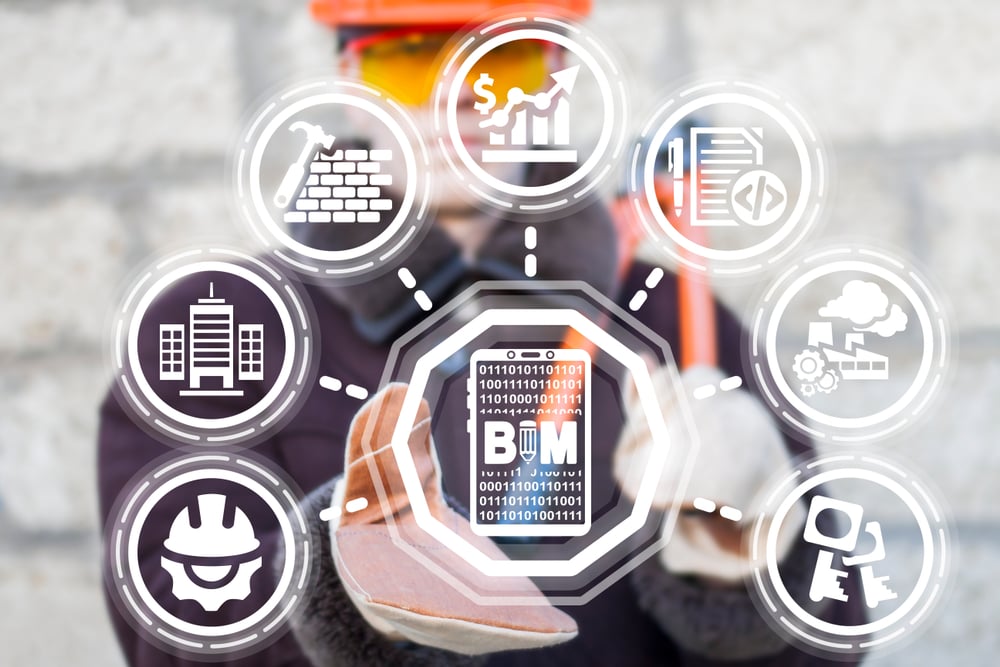
Modular construction is a method in which structural units or modules are fabricated off site in manufacturing plants, to then be transported and assembled on the construction site. Prefabricated modules are completed with mechanical, electrical, and plumbing (MEP) fixtures, and this procedure can take place both offsite and onsite. The use of modular construction provides multiple advantages over traditional construction, such as the following:
- Shortening of project schedules
- Better product quality
- Increased site safety
- Less workers are required
- Reduction in environmental impact, noise and air pollution
As mentioned above, modular units are equipped with MEP systems installed onsite or in manufacturing plants. However, the coordination and fabrication of these systems has always been a challenge for construction professionals. The design challenges include:
- Determining the optimal distribution of MEP systems in crowded spaces
- Avoiding interference among building systems
- Complying with diverse design and operation criteria
Building Information Modeling (BIM) software is a powerful tool when designing MEP systems for modular construction. BIM can be used for coordination and documentation when fabricating MEP systems. This way, construction firms can improve quality while cutting costs.
Building Information Modeling
BIM software provides a platform for construction professionals to create digital models. The design, construction schedule, cost, and life cycle of a structure can be analyzed and simulated automatically. BIM allows design engineers, architects and construction contractors to visualize the entire scope of a project - they can focus on the important decisions as tedious tasks are automated.
BIM Innovations and Improvements for MEP Modular Construction
As mentioned before, there are four dimensions for each building model: design (3D) and schedule (4D). However, the modern design approach for buildings also considers cost (5D) and life cycle (6D).
Design
BIM allows professionals to create and visualize a building model in 3D. This can be performed for an entire building, or individual modules. With these models, users can analyze geometries, locations, clearances and relative positions in a way that is not possible with 2D blueprints.
When using BIM for modular construction projects, the most valuable advantage is facilitating collaboration and communication. BIM is particularly useful when working with construction documents, rapid prototypes, exterior envelopes, interior finishing, and MEP fixtures.
Reduce project costs with modular construction.
BIM software can identify conflicts, interference and collisions between MEP systems prior to fabrication, while all project participants are working simultaneously. This is a major benefit: interferences can be represented in 3D models rather that traditional methods like overlaying drawings, or even worse, during the installation process. Once the model is completed, drawings can be easily generated, minimizing change orders and material waste.
Schedule
BIM systems simplify scheduling during the design and construction phases. Through BIM tools, users can link construction schedules to individual building systems or components, to plan the sequence of critical activities. Effective scheduling accelerates the project, allowing sections of MEP systems to be prefabricated and installed more quickly.
Cost
BIM can also automate cost estimation, and users can analyze how design decisions affect the total cost of a project. When generating 3D models, users can assign cost data to the materials or components used. Then, the cost information in the BIM model can be used to create estimates and track expenses.
Prior to the use of BIM software, cost estimates would be generated from quantity take-off using 2D drawings. BIM automates this process with 3D models, and the information is refreshed automatically when changes are applied. Under the traditional approach, design changes required the repetition of long calculations.
Life Cycle Analysis
Life cycle analysis is relatively new in BIM. It focuses on delivering modular buildings that are resource-efficient, environmentally sustainable, cost-effective, and pleasant for occupants throughout their life cycle.
Using BIM tools and the model created, modular buildings can be analyzed in an interactive format. BIM can be used for measures like green building materials, energy efficiency, natural lighting, water conservation, site assessment, indoor health, environmental impact reduction, sustainable operation, and maintenance.
Using BIM in a modular construction project provides multiple benefits. The project uses materials and labor more efficiently, since the entire process from planning to construction is better organized. Building Information Modeling allows for better design coordination and clash detection between systems. BIM even has marketing applications, since 3D models, renders, and animated walkthroughs can be used when presenting the project to clients.
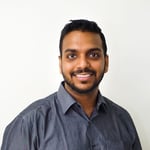
Anuj Srivastava
Anuj Srivastava is a principal partner at NY Engineers. He is known for his MEP franchise market knowledge. Anuj is currently leading a team of 100+ MEP/FP engineers and has successfully led over 1500 franchise projects in the US.
Join 15,000+ Fellow Architects and Contractors
Get expert engineering tips straight to your inbox. Subscribe to the NY Engineers Blog below.