What is Modular Construction? Types of Modular Construction
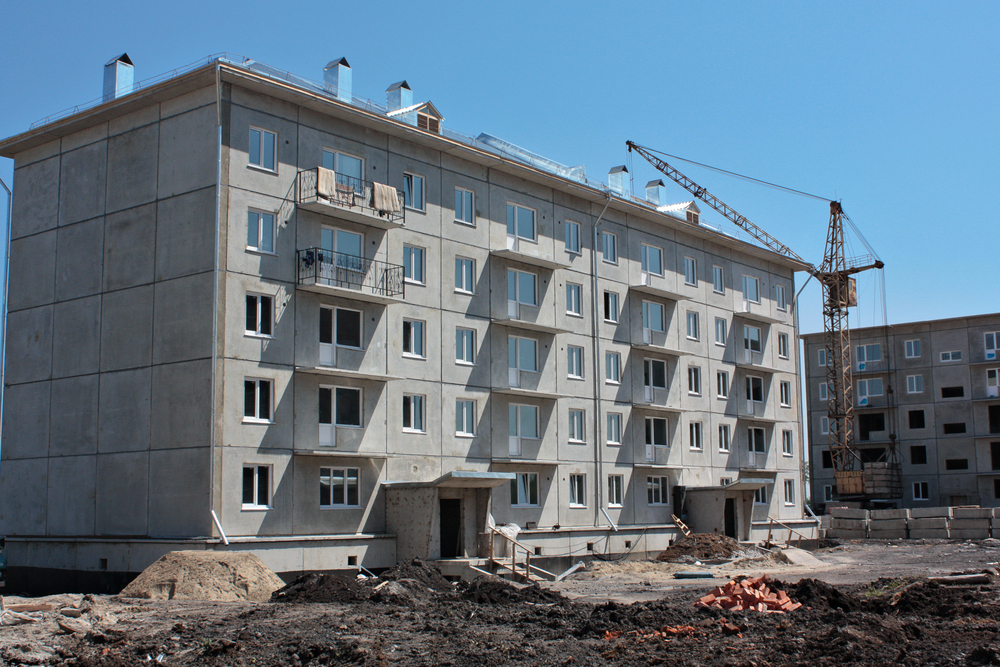
Modular construction is a process in which buildings are manufactured off-site in factories, under strict quality controls, but using the same building codes and standards as conventional construction methods. These buildings are made in modules or small parts, which are transported to the construction site and assembled. Modular construction is becoming more popular mainly due to its quick completion, cost-effectiveness and efficiency.
Types of Modular Construction:
1. Permanent Modular Construction (PMC)
Permanent modular construction is a sustainable building method, which uses lean manufacturing techniques to prefabricate single- or multi-story buildings in modular sections. PMC modules can be adapted to existing buildings or assembled by themselves. These modules can be completed with MEP appliances and interior finishes in less time than its site-built counterpart. Idylls was the first luxury condominium to use this concept in Manhattan, and NY Engineers delivered the MEP design.
2. Relocatable Buildings
Relocatable Buildings (RB) are partial or complete assemblies, fabricated in a manufacturing plant with a modular construction process. Although they are relocatable, these buildings meet building codes and state regulations. Relocatable buildings are designed to be reused multiple times and transported to various sites; they are not permanently affixed to real estate but are installed under manufacturer guidelines and local codes.
Some common applications include construction site offices, schools, medical clinics and points of sale. RBs offer ease of relocation, fast installation, low-cost reconfiguration, flexibility and accelerated depreciation for accounting purposes.
Benefits of Modular Construction
1.Faster Construction
Modular building projects are completed 30-50% times faster than those with conventional construction methods. This is because modular construction can proceed simultaneously with site and foundation work.
2.Elimination of Weather Delays
60-90% of the construction work is completed in a closed factory environment, and this mitigates the impact of unfavorable weather. With conventional construction methods, work must often be suspended completely on days with harsh weather conditions.
3.Quality Construction
Off-site construction allows a more effective enforcement of quality and safety guidelines. Building materials are protected from the weather during all stages of construction, which is a common cause of imperfections in outdoor projects. Modular buildings are completed under the same regulations, codes, and materials as conventional buildings.
4.Flexibility
Many modular buildings can be disassembled and relocated for new purposes, reducing the demand for raw materials and energy usage required for construction. Even if the the project used Permanent Modular Construction, recovering materials and modules is simpler than in a normal building.
5.Less Material Waste
Waste is eliminated by recycling and controlling inventories. Building materials are also protected from the weather since everything is kept inside the factory. Modular construction also makes it easier for construction workers to prevent waste, since there is greater control over project conditions.
6.Air Quality
Factory controlled settings allows materials to remain dry during all stages of construction. Therefore, the level of trapped moisture in new constructions is reduced, improving air quality. This helps control mold, dust mites and other organisms that thrive with moisture.
7.Safety
Working indoors allows a safer environment, it reduces risk and hazards present in construction sites. With conventional construction methods, work must often be performed at height or in uncomfortable positions where accidents are more likely.
8.Strength
Modular buildings are generally stronger than site-built structures because each module is designed to withstand transportation and lifting. Once together, the modules are securely joined into a whole integrated assembly.
9.Reduces Disruption
Since approximately 80% of the job is done offsite, modular construction allows business owners to continue working while renovations are being done. Modular construction also reduced disruption for the buildings surrounding the project site.
10.Eco-Friendly
Besides reducing waste, modular construction is leading the market in utilizing eco-friendly materials. A wider range of materials becomes available when the construction process can be completed under controlled factory conditions.
11.Cost-Effective
Affordability is a key feature of modular construction. When multiple similar pieces are being made all at one, cost and time savings are achieved with economies of scale. Modular construction is especially useful for projects with many identical buildings, since modules can be produced in series.
12.Acoustics
Modules are designed as independent units, and they can be soundproofed to block noise once they are assembled together.
Disadvantages of Modular Construction
The main disadvantages of modular construction apply in the housing sector, and they are summarized below.
Size
Modules must be transported from the factory to the construction site, and this must be planned correctly. The size and properties of each element must be considered, to determine a transportation method that will not cause damage. In the case of prefabricated homes, this can be a drawback because rooms are usually smaller than in conventional homes.
Financing
When financing modular homes, banks will normally issue a loan that goes through two stages. These are known as construction-to-permanent loans. In many cases, owners cannot get a traditional bank loan until construction on the home is complete. Financing the project upfront becomes a challenge in this case.
Land Restrictions
In some places, local authorities may not allow building modular homes. Therefore, it is important to learn about local laws before deciding to purchase.
Looking for cost effective custom modular building design?
Conclusion
Modular construction provides structurally strong buildings in less time than conventional construction methods. It also ensures high levels of quality control, reducing site disruption and vehicular traffic. Another benefit of modular construction is that it improves overall safety and security for workers.
It is important to consider all construction methods to determine which technique is the most suitable for your project. Offsite construction is generally chosen during the earlier stages of project planning to avoid further redesign. However, this does not limit the owner from redesigning a building originally intended for site construction into a modular version. If your main concern is using more sustainable construction methods, modular construction is definitely a technique to consider - it provides a controlled environment that reduces waste.
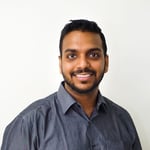
Anuj Srivastava
Anuj Srivastava is a principal partner at NY Engineers. He is known for his MEP franchise market knowledge. Anuj is currently leading a team of 100+ MEP/FP engineers and has successfully led over 1500 franchise projects in the US.
Join 15,000+ Fellow Architects and Contractors
Get expert engineering tips straight to your inbox. Subscribe to the NY Engineers Blog below.