Structural Engineering: Comparing Welded and Bolted Unions
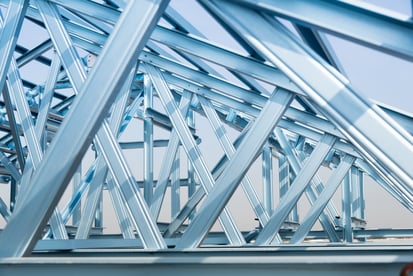
During the planning and design stage of any project, engineers must decide which material or tool is the best to complete certain tasks. The types of joints used in a structure usually depend on the overall design, but there are several factors to consider - cost, installation time and overall performance. This article compares welded joints and bolted joints, typically used to join elements made of metals or thermoplastics. Joint design is a key element in steel construction.
Welded joints consist on fusing two elements with extreme heat and allowing them to cool, and the construction industry uses various welding methods. According to the American Welding Society (AWS), a non-profit organization dedicated to the study and development of welding, there are five types: butt, corner, edge, lap and tee welding. These types of joints are determined by the position of welded elements relative to one another.
Bolted joints use fasteners that hold structural elements in a specific position, which are then secured with screw threads. Bolted joints are classified into tension joints and shear joints. Like in many engineering decisions, both options have advantages and disadvantages.
Keep your projects on track with construction management services.
Cost Comparison
The cost of bolted and welded joints varies by project, but bolted joints are usually the less expensive option. The price of bolted joints is more sensitive to steel prices, but their manufacturing process is more efficient and automated, compared with welded joints.
Welded joints can only be carried out by certified welders, and their hourly rates can be high. On the other hand, the labor cost associated with tightening bolts is much lower. If project cost is a key concern, bolted joints will normally be the best option.
Structural Performance Comparison
Welded joints are normally stronger than bolted joints, in great part because their material does not have the perforations needed for bolted joints. The manufacturing process is the determining factor when it comes to joint strength: bolted joints offer simplicity, but welded joints provide higher strength.
Welded joints are recommended when the structural performance of a project takes higher priority than cost.
Inspection Difficulty with Each Option
In bolted joints, inspectors must verify that the bolt stick-out is positive or zero - having the end of a bolt inside the nut is unacceptable. Inspectors must also ensure that bolts have been tensioned, and when necessary check if ends have been snapped off.
Welding inspection methods vary depending on the project. Visual inspection is the most common and it is carried out before, during and after welding. Other inspection methods require specialized equipment, which is more expensive and requires AWS certified inspectors. In other words, the inspection of welded joints has a higher cost and difficulty.
Joint Flexibility Comparison
Welded joints are more rigid than bolted joints, due to the continuity of the cross section. On the other hand, bolted joints are connected with plates or angles, and the deflection of these elements during load transfer adds flexibility. For this reason, bolted joints allow more movement with less structural stress.
A drawback with bolted joints is the additional hardware required for installation, and this limits their applications. Welding is more versatile, since nearly any two surfaces can be welded together, and new elements can be easily added to existing unions.
Installation Process and Safety
There are important differences between the installation procedures of bolted joints and welded joints. Construction managers must be aware of them to guide the project effectively.
Bolted joints are easier to handle, and are usually installed with an impact wrench or an ordinary spud wrench. They are also easier to repair, which can help save time in unexpected situations. Bolted joints also offer a faster installation in the field.
Welding is usually done manually by a certified welder. Different equipment types and energy sources are required, depending on the type of weld. Shielded metal arc welding (SMAW) is the most common, where an electric arc is produced between a coated metal electrode and the steel components to be welded. Welding can be carried out in a factory or at the project site, but there are strict safety and quality requirements in both cases.
Welding is a hazardous task and precautions are necessary to avoid burns, vision damage, inhalation of fumes and gases, UV radiation exposure, and electric shock. On the other hand, bolting has no specific risk other than working at height. Workplace safety is important regardless of the joint type, but welding comes with more task-specific risks.
Concluding Remarks
In conclusion, bolted joints have the advantage of cost and simplicity, but there is a loss of structural performance. On the other hand, welded joints are stronger but more expensive and difficult to handle.
No option can be considered superior that the other for all cases, since the best match changes depending on the project. At the end of the day, the type of joint specified will depend on project requirements and owner preferences.
Nearby EngineersNew York Engineers has a MEP design track record of 1,000+ projects. Contact us via email (info@ny-engineers.com) or phone (786) 788-0295212-575-5300, and make sure your building systems meet codes.
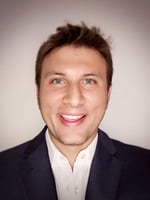
Michael Tobias
Michael Tobias, the Founding Principal of NY Engineers, currently leads a team of 150+ MEP/FP engineers and has led over 4,000 projects in the US
Join 15,000+ Fellow Architects and Contractors
Get expert engineering tips straight to your inbox. Subscribe to the NY Engineers Blog below.